Now You Know Hydroentanglement Bonding Process for Production of Nonwoven Fabric (Part-5)
Friday, 8 March 2019
Edit
Hydro-entanglement Bonding Process for Production of Nonwoven Fabric (Part-5)
Eng Mohamed Elsharkawy
Dept. of Textile Engineering
Alexandria University
Alexandria, Egypt
Email: m.elsharkawy.tex@gmail.com
Dept. of Textile Engineering
Alexandria University
Alexandria, Egypt
Email: m.elsharkawy.tex@gmail.com
CHAPTER 4
THE DESIGN OF MACHINE
THE DESIGN OF MACHINE
4.1. INTRODUCTION
As the name implies the process depends on jets of water working at very high pressures through jet orifices with very small diameters. A very fine jet of this sort is liable to break up into droplets, particularly if there is any turbulence in the water passing through the orifice. If droplets are formed the energy in the jet stream will still be roughly the same, but it will spread over a much larger area of batt so that the energy per unit area will be much less. Consequently the design of the jet to avoid turbulence and to produce a needle-like stream of water is critical. The jets are arranged in banks and the batt is passed continuously under the jets held up by a perforated screen which removes most of the water. Exactly what happens to the batt underneath the jets is not known, but it is clear that fiber ends become twisted together or entangled by the turbulence in the water after it has hit the batt. It is also known that the supporting screen is vital to the process; changing the screen with all other variables remaining constant will profoundly alter the fabric produced.
Although the machines have higher throughputs compared with most bonding systems, and particularly compared with a needle loom, they are still very expensive and require a lot of power, which is also expensive. The other considerable problem lies in supplying clean water to the jets at the correct pH and temperature. Large quantities of water are needed, so recycling is necessary, but the water picks up air bubbles, bits of fiber and fiber lubricant/fiber finish in passing through the process and it is necessary to remove everything before recycling. It is said that this filtration process is more difficult than running the rest of the machine.
4.2. The Hydro-entanglement prototype:
The machine consists of two main units:
1. Pump with high pressure up to 150 par :
The pump is the heart of the water jet system. The pump pressurizes the water and delivers it discontinuously and has ability to turn that pressurized water into a supersonic water jet stream.
Table (1) Specification of the pump
- The Derive unit
- The Hydro-entanglement unit
1. Pump with high pressure up to 150 par :
The pump is the heart of the water jet system. The pump pressurizes the water and delivers it discontinuously and has ability to turn that pressurized water into a supersonic water jet stream.
![]() |
Figure (4.1): Piston pump |
RPM | Model | Flow (l/min) | Pressure (bar) | Power (kw) | Weight | |
1450 | PNC 09/17 S | 9.0 | 170 | 2.9 | 5.3 | S = Male Shaft 24mm |
2. Motor to drive the pump
Specifications
![]() |
Figure (4.2): Motor |
Specifications | ||||
RPM: 1750 | Thermal Protection: On request | |||
Voltage: 230V | Enclosure: TEFC | |||
Phase: 1 | Service Factor: 1.0 | |||
Hertz: 60 | Frame: H112 | |||
Full Load Amps: 23 | Bearings: KBC 3606ZZ/1pcs | |||
Weight: 66 lbs | . |
The pump and the motor were connected by using (KE' SERIES ELASTOMERIC COUPLINGS). General purpose flexible coupling, excellent transmission capacities, are simple to be installed with low maintenance requirements.
Slots have been made in the coupling from two sides by using (vertical milling machine)[14]. From the side of the motor this slot is with dimension (8*4) and from the side of the pump with dimension (8*3).
And after that the coupling had been putted between the pump and the motor but there was a problem that the axes height of the pump is lower than the axes height of the motor and this will cause faults during working and will lead to damage the motor or the pump so four circular legs with ( 3 mm diameter and height 8 mm ) have been made , this legs make the two parts in the same level and after that we put them on a steel plate with dimension ( 75*35*10 ) and the plate is putted on a base and is fixed with the base by using electrical welding .
This has been made in the Military Mill no 10.
4.2.1. Laser Cutting Process:
The laser cutting process uses a focused laser beam and assists gas to sever metallic plate with high accuracy and exceptional process reliability. The laser beam is generated by a resonator, and delivered through the cutting nozzle via a system of mirrors [15].
![]() |
Figure (4.3): Coupling |
And after that the coupling had been putted between the pump and the motor but there was a problem that the axes height of the pump is lower than the axes height of the motor and this will cause faults during working and will lead to damage the motor or the pump so four circular legs with ( 3 mm diameter and height 8 mm ) have been made , this legs make the two parts in the same level and after that we put them on a steel plate with dimension ( 75*35*10 ) and the plate is putted on a base and is fixed with the base by using electrical welding .
This has been made in the Military Mill no 10.
![]() |
Figure (4.4) : Connection between pump and motor |
Related:
The advantages of laser technology :
Laser technology has the following advantages:
Most laser cutting is carried out using CO2 or Nd: YA Glasers. The general principles of cutting are similar for both types of laser although CO2 lasers dominate the market for reasons, which will be discussed later in the paper.
A laser beam delivery system is shown below, consisting of:
The focusing device consists of either a zinc-selenide lens or a parabolic mirror which brings the laser beam to a focus at a single point. Depending on the laser beam power, a power density of more than 107 W/cm2 is achieved at the focus point. The focal length gives the distance of the focal point from the focusing optics.
The focal point is positioned above, on or below the material surface according to the requirements of the material. The high power density results in rapid heating, melting and partial or complete vaporization of the material. The gas flowing from the cutting nozzle removes the molten mass from the kerf.
The machine moves the cutting head over the metal sheet according to the programmed contour, cutting the work-piece from the sheet.
Laser technology has the following advantages:
- High accuracy.
- Excellent cut quality.
- High processing speed.
- Small kerf.
- Very small heat-affected zone compared to other thermal cutting processes.
- Very low application of heat, therefore minimum shrinkage of the cut material.
- It is possible to cut complex geometrical shapes, small holes, and beveled parts.
- Cutting and marking with the same tool.
- Cuts many types of materials.
- No contact between the material and machining tool (focusing head) and therefore no force is applied to the work-piece.
- Easy and fast control of the laser power over a wide range (1-100%) enables a power reduction on tight or narrow curves
- The oxide layer is very thin and easily removed with laser torch cutting
- High-pressure laser cutting with nitrogen enables oxide-free cutting
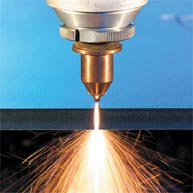
Most laser cutting is carried out using CO2 or Nd: YA Glasers. The general principles of cutting are similar for both types of laser although CO2 lasers dominate the market for reasons, which will be discussed later in the paper.
A laser beam delivery system is shown below, consisting of:
- CO2 laser resonator
- Rear mirror
- Gas excitation generates single wavelength light
- Output mirror
- Polarizing mirror
- Telescope mirror
- Beam bender
- Machine gantry
- Constant beam length carriage
- Beam bender
- Beam bender
- Cutting carriage
- Beam bender
- Adaptive mirror
- Window
- Focusing mirror
- Cutting head
- Cutting nozzle
![]() |
Figure (4.5): Laser cutting machine |
![]() |
Figure (4.6): Focusing device at cutting machine |
The machine moves the cutting head over the metal sheet according to the programmed contour, cutting the work-piece from the sheet.
Sumber http://textilelearner.blogspot.com