Now You Know Treatment of Cotton Fiber with Chitosan for the Improvement of Exhaustion during Dyeing with Reactive Dye (Part-5)
Sunday, 3 February 2019
Edit
Treatment of Cotton Fiber with Chitosan for the Improvement of Exhaustion during Dyeing with Reactive Dye (Part-5)
Mustaque Ahammed Mamun
Department of Textile Engineering
Dhaka University of Engineering & Technology (DUET)
Cell: +8801723300703
Email: mamuntex09@gmail.com
Department of Textile Engineering
Dhaka University of Engineering & Technology (DUET)
Cell: +8801723300703
Email: mamuntex09@gmail.com
Previous Part
CHAPTER 4
RESULTS AND DISCUSSIONS
RESULTS AND DISCUSSIONS
4.1. Measurement of Dye Exhaustion
Dye exhaustion may define as the leaving of a dye from the dye bath and attachment to the fiber being dyed. For instance, 70% exhaustion would mean that 70% of the total amount of dye has attached to the fiber, and 30% is still in solution. Dyebath exhaustion can be calculated as the mass of dye taken up by the material divided by the total initial mass of dye in the bath, for a bath of constant volume [21].
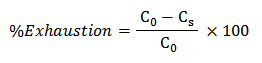
![]() |
Figure: 4.1 Dye exhaustion percentage of chitosan treated and untreated samples. |
4.2 Depth of Shade
Color depth of the dyed fabrics was analyzed by meauring the K/S values of samples. Higher the value of K/S more dye will absorb in the fabric. Color measuring instrument (spectrophotometer) determines the K/S value of a given fabric through Kubelka-Munk equation as follows [21].
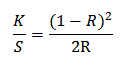
![]() |
Figure: 4.2 the gradual increment of dye absorption (K/S value) with the increment of chitosan concentration. |
4.3 Color Fastness properties
Table: 4.1 Fastness Rating of Rubbing.
Fabric Type | Rubbing Fastness | |
| Dry | Wet |
U | 4/5 | 4 |
A | 4/5 | 3/4 |
B | 4/5 | 3/4 |
C | 4/5 | 3/4 |
D | 4/5 | 3 |
E | 4/5 | 3 |
Table: 4.1 Fastness Rating of washing.
Fabric Type | Washing fastness | Color staining | |||||
| Color change | Acetate | Cotton | Nylon | Poly: | Acrylic | Wool |
U | 4/5 | 4/5 | 4/5 | 4/5 | 4/5 | 4/5 | 4/5 |
A | 5 | 4/5 | 4/5 | 4/5 | 4/5 | 4/5 | 4/5 |
B | 5 | 4/5 | 4/5 | 4/5 | 4/5 | 4/5 | 4/5 |
C | 5 | 4/5 | 4/5 | 4/5 | 4/5 | 4/5 | 4/5 |
D | 4/5 | 4/5 | 4 | 4/5 | 4/5 | 4/5 | 4/5 |
E | 4/5 | 4/5 | 4 | 4/5 | 4/5 | 4 | 4/5 |
Table: 4.2 Code of test samples
Test fabric type | Code |
Normal fabric without any chitosan treatment | U |
Fabric treated with 0.5% Chitosan solution | A |
Fabric treated with 1% Chitosan solution | B |
Fabric treated with 1.5% Chitosan solution | C |
Fabric treated with 2.5% Chitosan solution | D |
Fabric treated with 3% Chitosan solution | E |
Related:
CHAPTER 5
CONCLUSION
CONCLUSION
5.1 Conclusion
Reactive dyeing process has been completed at 600C and the added time remains 60 mins. Fixation and exhaustion have been completed at 600c. The addition of glubar’s salt is necessary as it increase the exhaustion of the dye bath. This study is intended to improve the absorption of reactive dye by cotton fiber after treating with chitosan. The application of chitosan on cotton fiber enhances the dye adsorption and also increases the hydroxyl group for fixation. Accordingly, dye exhaustion and depth of shade improve in the treated fabric compared to the untreated fabric. Though the fastness rating is lower in case of wet rubbing fastness, the overall fastness rating is satisfactory. In all cases, the pre-dyeing method in which the fabrics were treated with chitosan solutions prior to dyeing produced the optimum K/S value. An increase in chitosan concentration resulted in an increase in the dyeability of dye. This effect was associated with the presence of bonded chitosan through the chemical reaction of the chitosan aldehyde group with cellulose. Due to high absorbency, hydrolysis of dye is reduced which is helpful to protect the environment from pollution. So the treatment of cotton with chitosan can be an effective way for this purpose.
REFERENCES
- M. Lewin, “Handbook of Fiber Chemistry,” 3rd Edition, Taylor & Francis, New York, 2010.
- H. Q. Yu, M. Dang and C. W. Yu, “A Preliminary Study on Chemical Degumming of Jute and Kenaf Fibers,” Plant Fiber and Products, Vol. 25, No. 1, 2003, pp. 190- 192.
- P. Ghosh, A. K. Samanta and G. Basu, “Effect of Selec- tive Chemical Treatments of Jute Fiber on Textile-Re- lated Properties and Processible,” Indian Journal of Fi- bers &Textile Research, Vol. 29, No. 1, 2004, pp. 85-89.
- W.-M. Wang, Z.-S. Cai and J.-Y. Yu, “Study on the Che- mical Modification Process of Jute Fiber,” Journal of En- gineered Fibers and Fabrics, Vol. 3, No. 2, 2008, pp. 1- 11.
- E. P. G. Gohl and L. D. Vilensky, “Textile Science,” 2nd Edition, Longman Cheshire, New Delhi, 1983.
- V. A. Shenai, “Chemistry of Dyes and Principles of Dye- ing,” 4th Edition, Sevak, Mumbai, Vol. 2, 1983.
- Broadbent, A. D. (2001). Basic Principles of Textile Coloration. west Yorkshire , UK, England: Sosiety of dyers and Colourists.
- Hustsman. (2004, 06 02). Hustsman Textile Effects. Safety Data Sheet .
- Ingamells, W. (1993). Colour for Textile. West Yorkshire, School of Home Economics and Institutional Management, University of Wales, England: Society of Dyers and Colourists.
- Park, J., & Shore, J. (2004). Practical Dyeing (Vol. 2). West Yorkshire, UK, England: Society of Dyers and Colourists.
- Rebecca, R. B. (2005). Fibre Reactive Dyes with Improved Affinity and Fixation Efficiency.
- Tomasino, D. C. (1992). Chemistry & Technology of Fabric Preparation and Finishing. Raleigh, North Carolina State University, North Carolina: Department of Textile Engineering, Chemistry & Science College of Textile.
- Trotman, E. (1975). Dyeing and Chemical Technology of Textile Fibre (Fifth ed.). High Wycombe, London, England: Charles Griffin & Company Ltd.
- Chitosan And Improved Pigment Ink Jet Printing On Textiles
- Nasar Harun Momin, B. Text. (Textile Chemistry), DKTE’s Textile Engineering Institute, M. Sc. Tech. (Textile Chemistry), University Institute of Chemical Technology, 2003
Sumber http://textilelearner.blogspot.com