Now You Know Treatment of Cotton Fiber with Chitosan for the Improvement of Exhaustion during Dyeing with Reactive Dye (Part-4)
Sunday, 3 February 2019
Edit
Treatment of Cotton Fiber with Chitosan for the Improvement of Exhaustion during Dyeing with Reactive Dye (Part-4)
Mustaque Ahammed Mamun
Department of Textile Engineering
Dhaka University of Engineering & Technology (DUET)
Cell: +8801723300703
Email: mamuntex09@gmail.com
Department of Textile Engineering
Dhaka University of Engineering & Technology (DUET)
Cell: +8801723300703
Email: mamuntex09@gmail.com
Previous Part
3.3 Methods
3.3.1 Padding procedure
Before dyeing the cotton sample fabric is treated with 0.5 %, 1.0%, 1.5%, 2.5% &3.0% chitosans in the padding machine. After padding the sample fabric is dryed at 60 oc, 30min and then curing is done at 130 oc for 5 minutes.
3.3 Methods
3.3.1 Padding procedure
Before dyeing the cotton sample fabric is treated with 0.5 %, 1.0%, 1.5%, 2.5% &3.0% chitosans in the padding machine. After padding the sample fabric is dryed at 60 oc, 30min and then curing is done at 130 oc for 5 minutes.
![]() |
Figure: 3.1 Padding mangle machine |
3.3.2 Stock Solution Preparation
During the lab deep preparation a little amount of dyes and others chemicals are required. The measurement of a little amount dyes and chemicals are very complex.1 gm of dye has take and soluble in 100 ml of warm water and make 1% dye stock solution. Similarly 5% of Na2Co3 (Sodium carbonate), 10% gluber salt of stock solution have make. By the preparation of stock solution we can easily take required amount of dyes and chemicals from the stock solution by the following calculation.
3.3.3 Recipe Formulation
To perform the experiment, there have differences between salt & chitosan evaluation of self shade (NOVACRON R RED TS FN-3B). For 1% dyes with gluber salt & various amount of chitosan without salt such as 0.5%, 1%,1.5%, 2.50%, &3.0% chitosans are used and analyses with them. The standard recipe is following
3.3.4 Dyeing Procedure
At first untreated and chitosan treated sample has collected & take all auxiliaries and dyes from the stock solution in the dye bath and take water to maintain 1:10 liquor ratio therefore fabric is added in dye bath at room temperature and run 10 minute. Temperatures gradually increase (2o /min) up to 60 oC. Now sodium bicarbonate is added in dye bath for fixation of reactive dye from the stock solution of sodium bicarbonate and measure pH of dye bath and run 60 minute at 60 oC. Complete dyeing the dye liquor has drain.
3.3.5 After Treatment
Removal of hydrolysed and unreacted dye from the goods is a vital step after dyeing. The amount of unfixed dye remaining in a cotton fabric dyed with reactive dyes may have to be less than 0.002% owf. Although bleeding out of such a small amount during subsequent washing by the consumer will not significantly alter the depth of shade of the material, it can visibly stain adjacent white goods. This is usually unacceptable. The entire washing operation involves achieving a compromise between the effectiveness of removal of unfixed dye and the cost of the large volumes of water used, including the heating costs. Low liquor ratio washing saves water but gives less dilution of the washing liquors. To remove unfixed dyed required the material is operating at atmospheric pressure. It can possible to carry out soaping at temperatures 80 °C for 10 minute.
3.3.6 Color Fastness to Rubbing Test (ISO 105 X 12)
The fastness test to rubbing used on a variety of fabric to evaluate the transfer of surface dye from the test fabric when it is applied surface friction or rubber against a rough surface. Crock meter & Grey scale are used for this test. To cut the fabric size 10cm Ă— 4cm & The rubbing cloth size 50mm Ă— 50mm.The crocking cloth against which the sample is rubbed is white, bleach, but without finish and undyed cotton fabric. Rubbing time: 10 Cycle/10second.
Working procedure:
The resistance of the loss of color of any dyed or printed material to washing is referred to as its wash fastness. Rota Wash, Scissor, Stitch machine are for this test. To cut the Fabric size 10 cm × 4 cm & also Multi fiber fabric. The color fastness to washing is measured by ISO Recommendation No. 1 (ISO 105 C03). A rating of 1(poor) – 5 (excellent) was assigned to each of the six fiber strips on the fabric.
Recipe:
Working Procedure:
During the lab deep preparation a little amount of dyes and others chemicals are required. The measurement of a little amount dyes and chemicals are very complex.1 gm of dye has take and soluble in 100 ml of warm water and make 1% dye stock solution. Similarly 5% of Na2Co3 (Sodium carbonate), 10% gluber salt of stock solution have make. By the preparation of stock solution we can easily take required amount of dyes and chemicals from the stock solution by the following calculation.
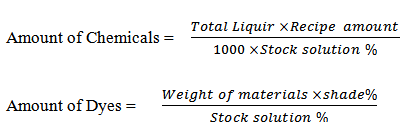
To perform the experiment, there have differences between salt & chitosan evaluation of self shade (NOVACRON R RED TS FN-3B). For 1% dyes with gluber salt & various amount of chitosan without salt such as 0.5%, 1%,1.5%, 2.50%, &3.0% chitosans are used and analyses with them. The standard recipe is following
Table: 3.8 Recipe for 1.0% (on the weight of fabric) shade without treatment the fabric with chitosan.
Ingredients | Without chitosan | Sample-1 | Sample-2 | Sample-3 | Sample-4 | Sample-5 |
Chitosan | 05% | 1% | 1.5% | 2.5% | 3% | |
Dyes (%) | 1.0 | 1.0 | 1.0 | 1.0 | 1.0 | 1.0 |
Salt (g/l) | 30 | 30 | 30 | 30 | 30 | 30 |
Soda ash (g/l) | 8 | 8 | 8 | 8 | 8 | 8 |
Wetting Agent (g/l) | 1.0 | 1.0 | 1.0 | 1.0 | 1.0 | 1.0 |
Leveling Agent (g/l) | 1.0 | 1.0 | 1.0 | 1.0 | 1.0 | 1.0 |
Sequestering agent | 1.0 | 1.0 | 1.0 | 1.0 | 1.0 | 1.0 |
M:L | 1:20 | 1:20 | 1:20 | 1:20 | 1:20 | 1:20 |
3.3.4 Dyeing Procedure
![]() |
Figure: 3.2 Infra Red Lab Dyeing Machine |
![]() |
Figure: 3.3 Dyeing Process |
3.3.5 After Treatment
Removal of hydrolysed and unreacted dye from the goods is a vital step after dyeing. The amount of unfixed dye remaining in a cotton fabric dyed with reactive dyes may have to be less than 0.002% owf. Although bleeding out of such a small amount during subsequent washing by the consumer will not significantly alter the depth of shade of the material, it can visibly stain adjacent white goods. This is usually unacceptable. The entire washing operation involves achieving a compromise between the effectiveness of removal of unfixed dye and the cost of the large volumes of water used, including the heating costs. Low liquor ratio washing saves water but gives less dilution of the washing liquors. To remove unfixed dyed required the material is operating at atmospheric pressure. It can possible to carry out soaping at temperatures 80 °C for 10 minute.
Related:
3.3.6 Color Fastness to Rubbing Test (ISO 105 X 12)
The fastness test to rubbing used on a variety of fabric to evaluate the transfer of surface dye from the test fabric when it is applied surface friction or rubber against a rough surface. Crock meter & Grey scale are used for this test. To cut the fabric size 10cm Ă— 4cm & The rubbing cloth size 50mm Ă— 50mm.The crocking cloth against which the sample is rubbed is white, bleach, but without finish and undyed cotton fabric. Rubbing time: 10 Cycle/10second.
![]() |
Figure: 3.4 Crock Meter |
- The rubbing arm is attached to the hook.
- Center a piece of abrasive paper, abrasive side up, on the base of the Crock meter.
- The paper’s long dimension should be in the direction of the rubbing.
- The specimen is placed flat and face-up on the abrasive paper. The specimen’s long dimension should be in the direction of the rubbing.
- A piece of test cloth is centered over the finger so that the weave is parallel with the direction of rubbing. Wrap the sides of the cloth evenly around the finger, making sure the cloth is smooth and taut over the finger’s rubbing area.
- The covered finger is then lowered onto the test specimen.
- The cycle counter is reset.
- The handle is turned at the rate of one turn per second for ten times. (Each back and forth motion of the arm equals one stroke and at a speed of 1 stroke/second.)
- After 10 strokes the specimen is removed and compared with the grays. The acceptable range is normally.This visual assessment is done in a color matching cabinet under standard lighting D65 (Artificial Daylight).
The resistance of the loss of color of any dyed or printed material to washing is referred to as its wash fastness. Rota Wash, Scissor, Stitch machine are for this test. To cut the Fabric size 10 cm × 4 cm & also Multi fiber fabric. The color fastness to washing is measured by ISO Recommendation No. 1 (ISO 105 C03). A rating of 1(poor) – 5 (excellent) was assigned to each of the six fiber strips on the fabric.
Recipe:
- Soap : 5 g/l
- Soda ash : 2 g/l
- Temperature : (60 ±2)0C
- Time : 30 min
- ML Ratio : 1:50
![]() |
Figure: 3.5 Washing and Dry Cleaning Color Fastness Tester |
- Stitch the specimen with multi fiber fabric in one side (length direction).
- Weight the specimen and calculate the volume of wash liquor required for ISO method given 150 ml liquor.
- Place the specimen in the container with the wash liquor.
- Run the machine and raise the temperature to 500C and run for 30 min.
- At the end of the test, place the specimen in the beaker and wash with 2 litter distilled water for 2 min & continuously starring the sample. Then washing in running tape water for 2 min. Excess water remove by hand squeezing.
- Dry the composite specimen in incubator, temperature not more than 600C. Then keep in relax for 1 hours.
Sumber http://textilelearner.blogspot.com