Now You Know 7 Tools of Quality Used in Garment Industry
Monday, 21 January 2019
Edit
SEVEN TOOLS OF QUALITY USED IN GARMENT INDUSTRY

R.S.BALAKUMAR
M.A. (SOCIOLOGY ), M.L.M.(Labour Management),
MBA (EXECUTIVE) in (FASHION-TECH), MISTE., Chennai, India
Cell: +91-9283182955
Email: rsbalakumar1953@gmail.com
SEVEN TOOLS OF QUALITY
Collecting and analyzing data is a foundation on which the effective management of quality rests. The so called “seven tool of quality” will help you effectively collect and analyze data.
The seven tools of quality are:
1. CAUSE AND EFFECT DIAGRAM:
This diagram shows a simple cause and effect diagram. This diagram is also called a fishbone diagram because it looks like skeleton of a fish. Also, this diagram is called Ishiwaka diagram, named after a Japanese quality expert who came up with this concept. The idea is first to identify and state the problem, which is an essence an effect of something that happened in a process, and think through various causes that may have resulted in an undesired effect. Drawing a cause and effect diagram helps one think systematically and logically. It graphically illustrates the relationship between a given outcome and all the factors that influence this outcome.
2. CHECK SHEET:
A check sheet is nothing but a form used to collect data in such a way that it makes not only the collection of data easy, but also the analysis of that data automatic. Each mark in the check sheet indicates a defect. The type of defects, number of defects, and their distribution can be seen at a glance, which makes analysis of data very quick and easy. Check sheets provide a logical display of data that are manually derived and yield results from which conclusions can be easily drawn.
3. CONTROL CHART:
A control chart is a simple graph or chart with time on the horizontal (X) axis vs. The quality characteristic measured on a vertical (Y) axis, with the control limits for the quality characteristic measured. In other words, a control chart is a continuous graphic indication of the state of a process with respect to a quality characteristic being measured. Let us say you are performing the final inspection of garments. You go out on the production floor and just before shipping pull a number of samples, inspect them, and note the number of defects, and calculate percent defective for several days. The results may look something like the following:
Variations or fluctuations in data are generally caused by a large number of small differences in materials, equipment, the surrounding atmospheric conditions, physical and mental reactions of people involved etc. These small differences cause data to fluctuate or vary in a manner called “normal” or “random” and such variations normal to the process.
Occasionally, however, there will be a larger or unusual difference, much more important than all those small differences put together. For example, material is taken from a different lot, the machine setter makes a new setting, an inexperienced operator takes the place of an experienced operator etc. These large differences cause changes in a manner called “abnormal” and these variations are called abnormal variations. In other words, these are variations that are not normal to the process.
Experience has shown that there are definite detectable differences between “normal” or “natural” variations and “abnormal” or “unnatural” variations. It is possible to detect this difference or to make this distinction using a statistical tool known as the control chart. Abnormal or unnatural variations have identifiable, assignable causes. This makes the diagnosis and correction of many production troubles and often brings substantial improvements in product quality and reduction in scrap and rework. Normal or natural variations have no assignable causes. So by identifying certain quality variations as having no assignable causes or being natural to the process, the control charts tells us when to leave a process alone and thus prevents unnecessarily frequent adjustments that tend to increase the variability of the process rather than decrease it.
4. FLOW CHART:
A flow chart is a schematic diagram of a process including all the steps or operations in the sequence as they occur. The logic here is that the act of constructing a flow chart will help you clarify various steps involved in a process and result in a better overall understanding of that process. One must understand a process clearly to be better able to identify and solve its problems. Flow chart can help understand the complete process, identify the critical stages of a process, locate problem areas, and show relationships between different steps in a process.
5. HISTOGRAM:
A histogram is a bar chart or a bar graph. It is graphical depiction of a number of occurrences of an event. For example, if you were to draw a histogram of the data. A histogram simply shows the distribution of sample data and gives some idea about variability of that data. Histogram is a graphic summary of variation in a set of data, and is a simple but powerful tool for elementary analysis. A histogram can help understand the total variation of a process, and quickly and easily determine the underlying distribution of a process.
6. PARETO CHART:
A Pareto chart is nothing but a histogram where a number of recurrences of an event are arranged in descending order. For example, a Pareto chart of the data contained.
Dr. Joseph M.Juran, the world famous quality management expert, observed in mid 1920s, as a young engineer, that quality defects are unequal in frequency, that is, when a long list of defects is arranged in order of frequency, generally, relatively few of the defects account for the bulk of defectiveness. Dr.Juran named this phenomenon the pareto principle. Thus, Pareto chart helps identify those defects that cause most problems, and by addressing those defects, most of the quality problems can be solved and improvement be made. For example, of the 208 defects shown, 45 or 21.6% are fabric defects. So in this instance, it would be most effective to address fabric quality first because any improvement in fabric quality will significantly improve overall quality of the product. The next defect to address should be open seams, and so forth.
7. SCATTER DIAGRAM:
A scatter diagram is a plot of one variable vs. another variable which is dependent on the first variable. For example, yarn strength may depend on twists per inch (twists per centimetre); moisture absorbency in a fabric may depend on fabric thickness, and so on. By plotting one variable against another, it may or may not become obvious how they are related; in other words, a pattern may or may not emerge.
Reference-
Managing Quality control in Apparel Industry Book - Pradeep.v. Mehtha.
The seven tools of quality are:
- Cause and effect diagram
- Check Sheet
- Control chart
- Flow Chart
- Histogram
- Pareto chart
- Scatter Diagram
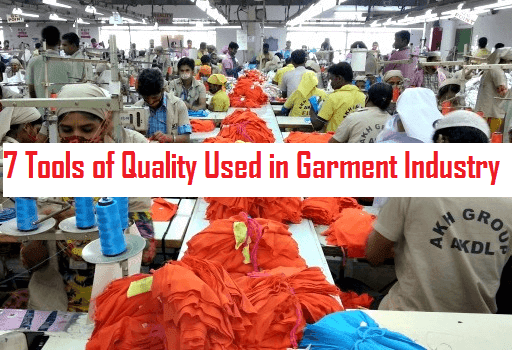
1. CAUSE AND EFFECT DIAGRAM:
This diagram shows a simple cause and effect diagram. This diagram is also called a fishbone diagram because it looks like skeleton of a fish. Also, this diagram is called Ishiwaka diagram, named after a Japanese quality expert who came up with this concept. The idea is first to identify and state the problem, which is an essence an effect of something that happened in a process, and think through various causes that may have resulted in an undesired effect. Drawing a cause and effect diagram helps one think systematically and logically. It graphically illustrates the relationship between a given outcome and all the factors that influence this outcome.
2. CHECK SHEET:
A check sheet is nothing but a form used to collect data in such a way that it makes not only the collection of data easy, but also the analysis of that data automatic. Each mark in the check sheet indicates a defect. The type of defects, number of defects, and their distribution can be seen at a glance, which makes analysis of data very quick and easy. Check sheets provide a logical display of data that are manually derived and yield results from which conclusions can be easily drawn.
3. CONTROL CHART:
A control chart is a simple graph or chart with time on the horizontal (X) axis vs. The quality characteristic measured on a vertical (Y) axis, with the control limits for the quality characteristic measured. In other words, a control chart is a continuous graphic indication of the state of a process with respect to a quality characteristic being measured. Let us say you are performing the final inspection of garments. You go out on the production floor and just before shipping pull a number of samples, inspect them, and note the number of defects, and calculate percent defective for several days. The results may look something like the following:
Variations or fluctuations in data are generally caused by a large number of small differences in materials, equipment, the surrounding atmospheric conditions, physical and mental reactions of people involved etc. These small differences cause data to fluctuate or vary in a manner called “normal” or “random” and such variations normal to the process.
Occasionally, however, there will be a larger or unusual difference, much more important than all those small differences put together. For example, material is taken from a different lot, the machine setter makes a new setting, an inexperienced operator takes the place of an experienced operator etc. These large differences cause changes in a manner called “abnormal” and these variations are called abnormal variations. In other words, these are variations that are not normal to the process.
Experience has shown that there are definite detectable differences between “normal” or “natural” variations and “abnormal” or “unnatural” variations. It is possible to detect this difference or to make this distinction using a statistical tool known as the control chart. Abnormal or unnatural variations have identifiable, assignable causes. This makes the diagnosis and correction of many production troubles and often brings substantial improvements in product quality and reduction in scrap and rework. Normal or natural variations have no assignable causes. So by identifying certain quality variations as having no assignable causes or being natural to the process, the control charts tells us when to leave a process alone and thus prevents unnecessarily frequent adjustments that tend to increase the variability of the process rather than decrease it.
4. FLOW CHART:
A flow chart is a schematic diagram of a process including all the steps or operations in the sequence as they occur. The logic here is that the act of constructing a flow chart will help you clarify various steps involved in a process and result in a better overall understanding of that process. One must understand a process clearly to be better able to identify and solve its problems. Flow chart can help understand the complete process, identify the critical stages of a process, locate problem areas, and show relationships between different steps in a process.
5. HISTOGRAM:
A histogram is a bar chart or a bar graph. It is graphical depiction of a number of occurrences of an event. For example, if you were to draw a histogram of the data. A histogram simply shows the distribution of sample data and gives some idea about variability of that data. Histogram is a graphic summary of variation in a set of data, and is a simple but powerful tool for elementary analysis. A histogram can help understand the total variation of a process, and quickly and easily determine the underlying distribution of a process.
Related:
A Pareto chart is nothing but a histogram where a number of recurrences of an event are arranged in descending order. For example, a Pareto chart of the data contained.
Dr. Joseph M.Juran, the world famous quality management expert, observed in mid 1920s, as a young engineer, that quality defects are unequal in frequency, that is, when a long list of defects is arranged in order of frequency, generally, relatively few of the defects account for the bulk of defectiveness. Dr.Juran named this phenomenon the pareto principle. Thus, Pareto chart helps identify those defects that cause most problems, and by addressing those defects, most of the quality problems can be solved and improvement be made. For example, of the 208 defects shown, 45 or 21.6% are fabric defects. So in this instance, it would be most effective to address fabric quality first because any improvement in fabric quality will significantly improve overall quality of the product. The next defect to address should be open seams, and so forth.
7. SCATTER DIAGRAM:
A scatter diagram is a plot of one variable vs. another variable which is dependent on the first variable. For example, yarn strength may depend on twists per inch (twists per centimetre); moisture absorbency in a fabric may depend on fabric thickness, and so on. By plotting one variable against another, it may or may not become obvious how they are related; in other words, a pattern may or may not emerge.
Reference-
Managing Quality control in Apparel Industry Book - Pradeep.v. Mehtha.
Sumber http://textilelearner.blogspot.com