Now You Know Hydroentanglement Bonding Process for Production of Nonwoven Fabric (Part-8)
Friday, 8 March 2019
Edit
Hydro-entanglement Bonding Process for Production of Nonwoven Fabric (Part-8)
Eng Mohamed Elsharkawy
Dept. of Textile Engineering
Alexandria University
Alexandria, Egypt
Email: m.elsharkawy.tex@gmail.com
Dept. of Textile Engineering
Alexandria University
Alexandria, Egypt
Email: m.elsharkawy.tex@gmail.com
Previous Part
CHAPTER (6)
RESULTS & DISCUSSION
RESULTS & DISCUSSION
After the experiments we have done on the geo-textile fabric, we find that the effect of weight change on fabric mechanical and filtration properties (hydraulic).
Weight of the fabric is an indicator of mechanical performance only within specific groups of textile, but not between one type of construction and another.
Therefore, it is impossible to use weight alone as a criterion in specifying textiles for civil engineering use. However, in combination of specified factors, weight is a useful indication of the kind of product for a particular purpose.
1. Fabric thickness
600 | 400 | 200 | Sample code |
3.292 | 2.875 | 1.9 | Thickness(mm) |
![]() |
Fig 6.1. |
- sample weight 200
- sample weight400
- sample weight600
600 | 400 | 200 | Sample code |
611.3 | 408 | 210.67 | Weight(gm/mt^2) |
![]() |
Fig.6.2. |
At machine direction
600 | 400 | 200 | Sample code |
71.74 | 35.02 | 7.64 | Tensile strength (kgf) |
88.67 | 78.33 | 132.67 | Elongation% |
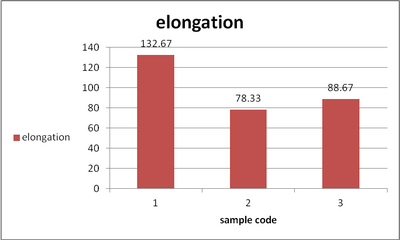
![]() |
Fig.6.3 |
600 | 400 | 200 | Sample code |
45.84 | 30.18 | 13.98 | Tensile strength (kgf) |
82.33 | 70.67 | 149.33 | Elongation% |
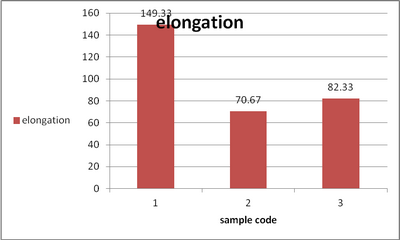
![]() |
Fig.6.4 |
- As it is universally to describe the strength of the fabric and show the load at break and elongation at break.
- At tensile strength, sample code3 with weight 600 gives the highest strength in both cases (machine direction-cross machine direction) and at the same time it gives the lowest value of elongation.
- But, sample code 1with weight 200 gives the lowest strength and the highest elongation.
600 | 400 | 200 | Sample code |
58.3 | 56.3 | 23 | Tear strength (kgf) |
![]() |
Fig.6.5 |
600 | 400 | 200 | Sample code |
33.66 | 32.14 | 24.58 | Puncture strength (kgf) |
![]() |
Fig .6.6 |
- It gives a simulation for working conditions fabric.
- At tear strength and puncture strength, due to fiber in cohesion the fabric strength is produced. So, samplecode3 with weight 600 gives the highest value of both and sample code1with weight 200 gives the lowest value of both.
600 | 400 | 200 | Sample code |
20.67 | 14.67 | 15.67 | Water head (cm) |
![]() |
Fig 6.7 |
It can vary immensely as it depends on the fabric construction. And it is necessary that water should flow freely through the geo-textile and prevent from unnecessary pressure.
7. Apparent opening size
600 | 400 | 200 | Sample code |
0.35 | 0.3 | 0.075 | AOS (mm) |
![]() |
Fig .6.8 |
It gives an indication of the amount and size of particles which can pass through the fabric during usage.
At water permeability and apparent opening size, sample 200 can easily pass any particles and water due to its high porosity, but sample 600 is difficult to let particles or water to flow through it.
From the results, we can see that the effect of weight of three different samples and the change happened in different properties. The meaning of changing weight is changing in fabric construction and this change the fabric properties.
In case of weight increase, the number of fibers increase and the friction between them too. This, in fact gives variable values for each sample.
CHAPTER (7)
CONCLUSION
Related:
In this project, we study two parts and they are:
- Hydro-entanglement machine for bonding non-woven.
- Experiments and testing geo-textiles.
So, we can summarize the main parameters in its design as followed:
Parameters of water jets:
- Density of jets: 10 – 30 jets/cm
- Jet diameter: 80 – 800 mm
- Pressure inside the jet manifold:
- up to 60 MPa for web bonding (Fleissner)
- up to 25 MPa for web patterning (Perfojet)
- Velocity of water jet: 10 – 350 m/sec
Typical water purification system has following stages:
- air separator,
- coarse filter, fine filter
- de-ionization unit,
- heat exchanger,
- bacteria filter.
We found that the properties increase with weight increase.
Geo-textiles are used in civil engineering earthworks to reinforce vertical and steep banks of soil, to construct firm bases for temporary and permanent roads and highways, to line ground drains, so that the soil filters itself and prevents soil from filling up the drainpipes and to prevent erosion behind rock and stone facing on river banks and the coast. They have been developed since the mid 1970s, but the advent of knitted and composite fabrics has led to a revival in attempts to improve textile construction in a designed fashion. Better physical properties can be achieved by using more than one fabric and by utilizing the best features of each.
CHAPTER (8)
REFERENCES
REFERENCES
- Pourdeyhimi B. (2005) Introducing to nonwovens, Lecture Notes of Introduction Nonwoven Products and Processes, North Carolina State University, NC.
- Medeiros F. J. (1997) Spun-lacing offers Utmost Versatility, American Textiles International, and November: 34-36.
- The Nonwovens Handbook (1988) INDA, Association of the Nonwoven Fabrics Industry.
- Vuillaume, Andre M.: A Global Approach to the Economics and End Product Quality of Spunlace Nonwovens, Tappi Journal, v.74, Aug '91, 149-152.
- White, C. F.: Hydro-entanglement Technology Applied to Wet Formed and Other Precursor Webs, TAPPI Nonwovens Conference, 1990, 177-187
- Jaussaud, Jean Paul: Rotary hydraulic Entanglement Technology, Nonwovens in Medical and Healthcare Applications Conference, Nov 10th -12th 1987, Brighton, England.
- Allen, Charles H., Jr.: New Development for Spun-lacing Cotton, Paper presented at Fiber Society Conference, University of Tennessee, and Knoxville 19th-21st Oct. 1997
- Widen, Christian B.: Forming Fabrics for Spunlace Applications, Tappi Journal, v.74, May '91, 149-153
- Information brochure for Hydro-entanglement technology from Valmet Paper Machinery, Honeycomb Systems Inc.
- (Hsu-Yeh Huang & Xiao GAO) M. G. Kamathq, Atul Dahiya, Raghavendra R. Hegde. SPUNLACE (HYDROENTANGLEMENT)
- Spunlace Non-woven" Perfojet, December 1991
- " The study on the mechanical properties of spun-laced nonwoven" 16th polymer symposium Vol.9, PP 433-436.
- Christian B. Widen, "Forming fabrics for spun-lace applications" TAPPI Journal, May 1991 un.1993,
- Connolly, T.J., Parent, L.R.: Influence of Specific Energy on the Properties of Hydro-entangled Nonwoven Fabrics, Tappi Journal, v.76, Aug '93, 135-141
- http://www.atlanticbearings.co.uk/couplings.html[15]
- http://www.technologystudent.com/equip1/vert1.htm [16]
- http://www.esab-cutting.com/products/laser-cutting-process.html
Sumber http://textilelearner.blogspot.com