Now You Know Garment Washing: An Effective Process for Beautification of Garments (Part-2)
Monday, 4 February 2019
Edit
Garment Washing: An Effective Process for Beautification of Garments (Part-2)
Rahat Khan
Dept. of Apparel Manufacturing
Atish Dipankar University of Science and Technology
Cell: +8801717781833
Email: rahat.info@gmail.com
Dept. of Apparel Manufacturing
Atish Dipankar University of Science and Technology
Cell: +8801717781833
Email: rahat.info@gmail.com
Previous Part
2.3.1 Garments washing machine:
The main function of garments washing machine is to remove the Starch and to make the garments soft. If any dirt is generated in the fabric surface it can be removed by washing. It gives garments new outlook.
Specification of machine:
2.3.2 Hydro extractor:
Hydro extractor is used to remove excessive water from the garments. Knitted fabrics should not be squeezed in pressure mangles. Hydro extractor is used for such kind of fabrics to remove excess water before go for drying. Hydro extraction is a batch process which works on centrifuge principle. Fabrics put into the perforated case, made for copper or galvanized iron, which is mounted on a central spindle and contained in steel or iron casing. When the perforated casing rotates at high speed, a centrifugal force is developed which forces the wet fabrics to the inner wall of the case. Water is then forced out from the fabrics through the perforation of the casing. It is the best process for removing water giving the most efficiency.
2.3.3 Drying machine:
After hydro extraction the garments are turned to drying machine for better drying .Tumble dryer is specially used for garments drying. Here the fabrics are dried at maximum relaxation state. That’s why shrinkage and GSM can be controlled.
2.3.4 Boiler:
Boiler is an essential machine, which is used in dyeing & washing industries to produce steam from water. It contains huge amount of water in it and convert those water in to steam to raise temperature.
The equipment used for producing steam is called steam generator or boiler. The boiler used for producing steam in IAL is Cochran boiler which is a fire tube type boiler. Simple vertical boiler of fire tube type is mainly used in small plant requiring small quantity of steam and where floor area is limited.
Here, gas is fed to the burner which run by thermo motor and produce flame. The flame produces hot flue gases, which pass through the tubes that are surrounded by water. This water is supplied from the soft water tank to the feed water tank, which is situated above the boiler. The heat energy of the flue gas is transfer to water which is converted into steam. This steam is supplied to the whole plant. The spent gases are then discharged to the atmosphere through chimney.
2.3.5 Sample washing machine:
After getting order from buyer, sample is prepared as per buyers’ requirement to match the original sample. Before bulk production this is done in sample washing machine.
2.3.6 Sand blasting unit:
It is a mechanical process of producing fading effect on garments made from heavy fabric like denim. Normally sand blasting is combined with wash like normal wash, bleach wash, enzyme wash & over dyeing.
The process of sand blasting is described below:
Aluminum oxide is used for sand blasting which looks like sand .This aluminum oxide are blown at very high pressure through a gun .The gun has a switch to start and stop flow of aluminum oxide .The garments to be sand blasted are placed on the bed of a closed chamber .From feeding chamber sands are blown by high air pressure through the pipe and gun .The area of the garments fabrics surface is faded by the friction affect of sand .The blow of sand is placed at 10-20 angle on surface .Fading is done on re marked areas .Various patterns or designs may be used during fading creation in the pre marked areas by blocking or fading technique .The faded garments are manually cleaned by shaking and kept aside
3.1 Sample preparation:
Denim:
Denim is a strong, durable fabric constructed in a twill weave with indigo and white yarns. The blue or indigo yarns are the length wise or “warp” threads (parallel to the selvedge). The white yarns run across the fabric width (the weft threads). Denim is traditionally woven with 100% cotton yarn; however, today it is blended with polyester, to control shrinkage & wrinkles, and lycra to add stretch.
Today, denim has many faces. It can be printed, striped, brushed, napped & stone washed, and the indigo blue yarn can be replaced with different colors’ to create colored denim.
3.2 Denim fabric analysis:
By analyzing the denim fabric with counter glass & needle we find that it is a 2 up 1 down twill weave fabric.
Fabric composition:
1. Warp: 100% cotton
2. Weft:
The main function of garments washing machine is to remove the Starch and to make the garments soft. If any dirt is generated in the fabric surface it can be removed by washing. It gives garments new outlook.
![]() |
Fig-1: Vertical washing machine |
![]() |
Fig-2: Horizontal washing machine |
- Capacity: 500kg (weight of garments)
- Normal capacity: 200kg
- Dia of main cylinder: 4-6 inch
- Height of the bar: 4inch
- Cylinder rpm: 30-40
- M: L: 1:5 to 1:10
2.3.2 Hydro extractor:
Hydro extractor is used to remove excessive water from the garments. Knitted fabrics should not be squeezed in pressure mangles. Hydro extractor is used for such kind of fabrics to remove excess water before go for drying. Hydro extraction is a batch process which works on centrifuge principle. Fabrics put into the perforated case, made for copper or galvanized iron, which is mounted on a central spindle and contained in steel or iron casing. When the perforated casing rotates at high speed, a centrifugal force is developed which forces the wet fabrics to the inner wall of the case. Water is then forced out from the fabrics through the perforation of the casing. It is the best process for removing water giving the most efficiency.
![]() |
Fig-3: Hydro extractor |
After hydro extraction the garments are turned to drying machine for better drying .Tumble dryer is specially used for garments drying. Here the fabrics are dried at maximum relaxation state. That’s why shrinkage and GSM can be controlled.
2.3.4 Boiler:
Boiler is an essential machine, which is used in dyeing & washing industries to produce steam from water. It contains huge amount of water in it and convert those water in to steam to raise temperature.
The equipment used for producing steam is called steam generator or boiler. The boiler used for producing steam in IAL is Cochran boiler which is a fire tube type boiler. Simple vertical boiler of fire tube type is mainly used in small plant requiring small quantity of steam and where floor area is limited.
Here, gas is fed to the burner which run by thermo motor and produce flame. The flame produces hot flue gases, which pass through the tubes that are surrounded by water. This water is supplied from the soft water tank to the feed water tank, which is situated above the boiler. The heat energy of the flue gas is transfer to water which is converted into steam. This steam is supplied to the whole plant. The spent gases are then discharged to the atmosphere through chimney.
2.3.5 Sample washing machine:
After getting order from buyer, sample is prepared as per buyers’ requirement to match the original sample. Before bulk production this is done in sample washing machine.
![]() |
Fig-4: Sample washing machine |
It is a mechanical process of producing fading effect on garments made from heavy fabric like denim. Normally sand blasting is combined with wash like normal wash, bleach wash, enzyme wash & over dyeing.
![]() |
Fig-5: Sand blasting unit |
Aluminum oxide is used for sand blasting which looks like sand .This aluminum oxide are blown at very high pressure through a gun .The gun has a switch to start and stop flow of aluminum oxide .The garments to be sand blasted are placed on the bed of a closed chamber .From feeding chamber sands are blown by high air pressure through the pipe and gun .The area of the garments fabrics surface is faded by the friction affect of sand .The blow of sand is placed at 10-20 angle on surface .Fading is done on re marked areas .Various patterns or designs may be used during fading creation in the pre marked areas by blocking or fading technique .The faded garments are manually cleaned by shaking and kept aside
![]() |
The process of sand blasting |
Chapter 3
Research methodology
Research methodology
3.1 Sample preparation:
Denim:
Related:
Today, denim has many faces. It can be printed, striped, brushed, napped & stone washed, and the indigo blue yarn can be replaced with different colors’ to create colored denim.
3.2 Denim fabric analysis:
By analyzing the denim fabric with counter glass & needle we find that it is a 2 up 1 down twill weave fabric.
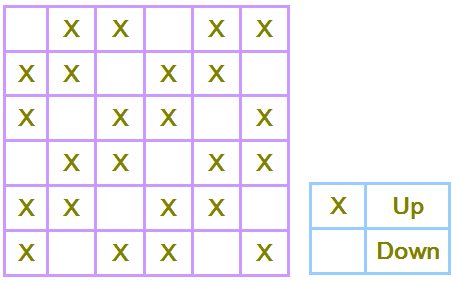
![]() |
Fig: Denim fabric sample |
1. Warp: 100% cotton
2. Weft:
- Cotton: 76%
- Polyester: 23%
- Spandex: 1%
- Total: 10
Sumber http://textilelearner.blogspot.com