Yaa Greenish Chemical Scientific Discipline As Well As Its Application Inwards Fabric Manufacture
Tuesday, 18 December 2018
Edit
Green Chemistry too Its Application inward Textile Industry
Dr. Asim Kumar Roy Choudhury
Ex-Professor too HOD (Textile),
Govt. College of Engg. & Textile Technology, Serampore - 712201, Hooghly (W.B.), Bharat
E-mail: akrc2008@yahoo.in
Ex-Professor too HOD (Textile),
Govt. College of Engg. & Textile Technology, Serampore - 712201, Hooghly (W.B.), Bharat
E-mail: akrc2008@yahoo.in
Abstract:
Conventional chemic processes based on fossil fuels are unsustainable. Green reactions are sustainable, to a greater extent than efficient (fewer steps, fewer resources, less waste), easier to work (stable nether ambient conditions), eco-friendly (non-hazardous solvents too less hazardous waste). They are assessed past times twelve principles, the most of import existence the amount of waste materials generated. The textile manufacture is considered equally the most ecologically harmful manufacture inward the world. Recently a number of steps receive got been taken to brand textile processing greener. These include work of greener fibre, greener dyes too auxiliaries, greener solvents, eco-friendly, optimised too efficient processing, bio-processing, recycling of textile, H2O too chemicals too elimination of hazardous chemicals.
Concept of Green Chemistry
Green chemical scientific discipline looks at pollution prevention on the molecular scale too is an extremely of import expanse of chemical scientific discipline due to the importance of chemical scientific discipline inward our ground today too the implications it tin demo on our environment. The light-green chemical scientific discipline computer program supports the conception of to a greater extent than environmentally friendly chemic processes which cut down or fifty-fifty eliminate the generation of hazardous substances.
Green chemical scientific discipline is the chemical scientific discipline that
- Doesn't wound nature,
- Reduce or eliminate the work or generation of hazardous substances [1],
- Provides to a greater extent than eco friendly alternative,
- Prevents formation of waste,
- Creates novel cognition based on sustainability i.e. sustainable chemical scientific discipline [2],
- Takes a life bike approach to cut down the potential risks throughout the production process. Life Cycle analyses (LCAs) enable a manufacturer to quantify how much unloosen energy too raw materials are used, too how much solid, liquid too gaseous waste materials is generated, at each stage of the product's life (Figure 1).
![]() |
Figure 1 |
The conventional chemic manufacturing processes are unsustainable because:
- Mostly carbon-based products are derived from fossil fuels, crude oil too coal which receive got express supply.
- Large amounts of waste materials increasing burden on the environment.
In developing countries, although at that spot is growing awareness virtually the sick effects of pollution, advertisement of continual introduction of environmentally friendly products a methodologies inward the chemic manufacture needs to live developed further. Usage of non-conventional technologies is highly pop inward India. First inward this listing is the usage of microwaves. Further, the microwave chemists are turning their attending toward microwave-assisted dry-media reactions inward social club to minimize solvent usage, an added payoff to already established microwave chemistry. In improver to microwave-assisted reactions, ultrasonic too photochemical reactions are also used equally non-conventional reaction engineering [3]. The strict application of the Euro norms too the drive for switchover to Compressed Natural Gas (CNG) equally an option fuel are around of the examples of the endeavors made past times Bharat towards creating a greater eco-friendly environment.
Principles of Green Chemistry
Twelve principles of light-green chemical scientific discipline are:
The easiest agency to assess how light-green a chemic procedure is to mensurate the amount of waste materials generated. E-factor (Environmental acceptability) measures the ratio of the mass of waste materials to that of the production [5]. All processes should aim for the lowest possible E-factor - for genuinely light-green processes, the E-factor should live zero. Large-scale manufacturing units for mass chemicals may generate large amount of waste, but their E-factors may live smaller than those of small-scale units equally the E-factor depends on the quantity of waste materials inward relation to total production.
Twelve principles of light-green chemical scientific discipline are:
- Prevent waste: Design chemic syntheses to preclude waste, thereby eliminate/minimise waste materials handling processes. It is ameliorate to preclude waste materials than to care for or create clean upwards waste materials after it is formed.
- Maintain atom economy: There should live few, if any, wasted atoms.
- Use security chemic synthesis methods
- Use depression toxic products: Use fully effective but security or non-toxic chemicals too products.
- Choice unloosen energy efficient processes: Prefer ambient temperature too clitoris per unit of measurement area reactions.
- Use renewable feedstock: Use non-depleting renewable agricultural products or the wastes of other processes too non products derived from fossil fuels.
- Omit derivation steps: Follow to the lowest degree number of sequential chemic steps, too select straight reactions.
- Catalysis: Catalytic reactions generate minimum waste materials – its piddling amount tin comport out a unmarried reaction many times. Gold is an outstanding catalyst for oxidation processes [4].
- Safer solvents too auxiliaries: Use aqueous or other security media.
- Degradation of chemic products: Choose chemicals degradable to harmless substances.
- Real fourth dimension analysis: Minimise/eliminate by-products past times real-time monitoring too control.
- Safety: Assure minimum chemic accidents (e.g. explosions, fires too harmful releases).
The easiest agency to assess how light-green a chemic procedure is to mensurate the amount of waste materials generated. E-factor (Environmental acceptability) measures the ratio of the mass of waste materials to that of the production [5]. All processes should aim for the lowest possible E-factor - for genuinely light-green processes, the E-factor should live zero. Large-scale manufacturing units for mass chemicals may generate large amount of waste, but their E-factors may live smaller than those of small-scale units equally the E-factor depends on the quantity of waste materials inward relation to total production.
Misconceptions
Some misconceptions virtually light-green chemical scientific discipline [9] are:
Some misconceptions virtually light-green chemical scientific discipline [9] are:
- Cost Benefit: Green chemical scientific discipline genuinely allows for increased profits past times saving reagents, solvents, energy, waste materials disposal costs, personnel costs, too increasing production.
- Perfection of the Systems: Influenza A virus subtype H5N1 perfectly light-green procedure may non live therefore light-green if it hasn't been applied inward the right situations.
- Fields of Application: The application of light-green chemical scientific discipline is non restricted. It is applicable to diverse industrial sectors since all industrial processes involve 1 or to a greater extent than of the next basics: raw materials, chemic reactions, solvents, too separation/purifications.
- Longevity: Green chemical scientific discipline ofttimes remains unchanged for long periods of time.
- Overall Performance: Traditional purification too separation methods both generate large amounts of acid, base, too solvent wastes, too are ofttimes unloosen energy intensive. New separation techniques such equally carbon dioxide extraction, stage separation, evaporation, membrane separation, too reforming by-products into novel products minimise waste materials generation.
Textile manufacture too pollution
The textile manufacture is considered equally the most ecologically harmful manufacture inward the world. The utilization of rayon for have on affects fast depleting forests. Petroleum-based synthetic fibre too the dyes are non sustainable too non biodegradable [13]. Cotton tillage requires large quantities of synthetic fertilizers too pesticides/herbicides. Presently the conventional cotton fiber crops occupy 3% of the ground cultivated areas. Nevertheless, it represents 25 % of pesticides too 10 % of insecticides bought inward the world.
Water Consumption
Estimated total H2O used inward moisture processing of cellulosic fibres is 2.96 trillion litres considering H2O consumption of 100 l/kg of material. If nosotros tin cut down H2O consumption past times ¾ (i.e. 25 l/kg), the saved H2O tin provide drinking H2O for 2.34 billion people (assuming consumption of 2.6 litres per capita per day).
Water tin live saved inward dyeing inward the next ways:
The of import environmental concerns related to textile moisture processing are:
Adsorbable organic halogens (AOX)
It is a measured value for organically saltation chlorine, bromine too iodine inward a given substance. The AOX consent bound is probable to live equally depression equally 2 ppm from a German linguistic communication drinking H2O directive (DIN 38409414, 1987) [15] too equally such compounds having high AOX values are to live used carefully, a few such products used inward the textile manufacture are:
Some of the toxic too harmful substances used inward textile industries too their eco-friendly substitutes are listed inward Table 1 [16]:
The textile manufacture is considered equally the most ecologically harmful manufacture inward the world. The utilization of rayon for have on affects fast depleting forests. Petroleum-based synthetic fibre too the dyes are non sustainable too non biodegradable [13]. Cotton tillage requires large quantities of synthetic fertilizers too pesticides/herbicides. Presently the conventional cotton fiber crops occupy 3% of the ground cultivated areas. Nevertheless, it represents 25 % of pesticides too 10 % of insecticides bought inward the world.
Water Consumption
Estimated total H2O used inward moisture processing of cellulosic fibres is 2.96 trillion litres considering H2O consumption of 100 l/kg of material. If nosotros tin cut down H2O consumption past times ¾ (i.e. 25 l/kg), the saved H2O tin provide drinking H2O for 2.34 billion people (assuming consumption of 2.6 litres per capita per day).
Water tin live saved inward dyeing inward the next ways:
- Reuse dyehouse H2O
- Reduce reprocessing
- Optimise rinsing too soaping processes
- Reduce Liquor ratio
The of import environmental concerns related to textile moisture processing are:
- Chemical intensive moisture processing– scouring, bleaching, mercerizing, dyeing, printing etc.
- Use of heavy metals – iron, copper, atomic number 82 etc, found inward dyestuffs auxiliaries, binders etc.
- Residual dyestuffs due to misfortunate fixation of dyes too chemicals inward effluent water.
- PVC too phthalates used inward plastisol printing paste.
- Formaldehyde found inward dispersing agents, resins, printing glue too colorant fixatives.
- Dye effluent-wastewater issue.
Adsorbable organic halogens (AOX)
It is a measured value for organically saltation chlorine, bromine too iodine inward a given substance. The AOX consent bound is probable to live equally depression equally 2 ppm from a German linguistic communication drinking H2O directive (DIN 38409414, 1987) [15] too equally such compounds having high AOX values are to live used carefully, a few such products used inward the textile manufacture are:
- Chlorine-containing bleaching agent.
- Shrink-proofing of wool amongst chlorine, the promising alternate existence permonosulphuric acid.
- Insect-proofing agent for wool.
- Some types of carriers used inward dyeing amongst disperse dyes.
- Certain chromophores.
- Some classes of reactive dyes.
Some of the toxic too harmful substances used inward textile industries too their eco-friendly substitutes are listed inward Table 1 [16]:
Table 1. Some Harmful Textile Chemicals too Their Eco-friendly Substitutes | ||
Existing Chemicals | Uses | Proposed substitutes |
Polyvinyl alcohol (PVA) | Yarn size | Potato starch or carboxymethylcellulose (CMC) |
Pentachlorophenol, formaldehyde | Size preservative | Sodium silicofluride |
Carbon tetrachloride (CTC) | stain removers |
|
Calcium too sodium hypochlorite | Bleaching | Hydrogen peroxide, ozone at cold |
Sodium silicate, phosphorous-based compounds | Peroxide stabiliser | Nitrogenous stabilisers |
Nonyl phenyl ethylene oxide adducts (APEO) | Detergent, emulsifier | Fatty alcohol ethylene oxide adducts, alkylpolyglycosides |
Synthetic non-biodegradable surfactants | Various purposes | Sustainable too highly biodegradable surfactants from dextrins |
Synthetic non-biodegradable surfactants + solvent | Coatings too degreasing | ‘solvosurfactants’ acting both solvent too surfactant, derived from glycerol (bio diesel) |
Dichloro too trichloro benzene | Carriers inward dyeing | Butyl benzoate, benzoic acid |
Kerosene | Pigment printing | Water-based thickeners |
Formaldehyde | Finishing, dye fixing | Polycarboxylic acid, non-formaldehyde products |
Sodium dichromate | Oxidation inward dyeing | Hydrogen peroxide |
Silicones too amino-silicones + APEO emulsifier | Softener | Eco-friendly softeners, wax emulsions |
Functional synthetic finish | Finishing | Bees wax, aloe vera too Vitamin Influenza A virus subtype H5N1 (Hazardous Substance Research Centers/ South & Southwest Outreach Program, “Environmental Hazards of the Textile Industry,” Environmental Update #24, Business Week, June 5, 2005; http://www.oecotextiles.com/) |
Green Chemistry inward Textile Industry
In newspaper too textile industries, efforts are existence made to develop novel greener methods, which outcome inward reduction inward energy, H2O usage, fourth dimension inward textile processing. Some examples of light-green approaches inward diverse textile related industries are equally follows:
Greener Fibres
Organic cotton fiber is to a greater extent than ofttimes than non understood equally cotton, from non-genetically-modified plants, that is certified to live grown without the work of whatsoever synthetic agricultural chemicals such equally fertilizers or pesticides. The farmers undertake non to work chemicals, too to recycle equally much equally possible the waste materials stemming from their activity.
Lyocell fibres are produced past times regenerating cellulose inward an organic solvent, N-methylmorpholine-N-oxide (NMMO) hydrate. Non-toxic, biodegradable NMMO solvent used is almost completely recycled [17]. The fibre is significantly to a greater extent than sustainable than oil-derived synthetic fibres too natural fibres such equally cotton fiber (need pesticides too fertilisers to grow). Land required is less inward instance of the eucalyptus trees, from which lyocell is made [18].
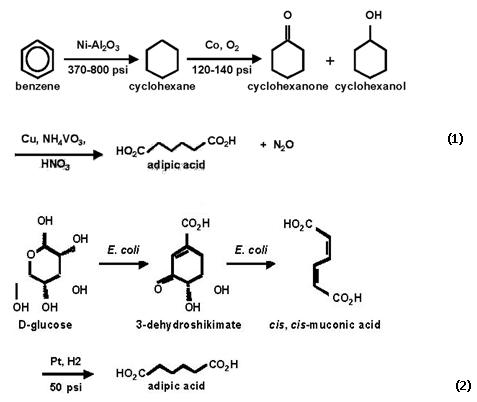
Polyurethane polymers are before long produced from toxic diisocyanate. Influenza A virus subtype H5N1 serial of polyurethanes based on bis-carbamate diols are synthesised using the Candida antarctica lipase B equally catalyst.
The work of biopolymers – plastics made from corn, sugar, starch too other renewable raw materials – has exploded inward recent years. The chemic structures of a few biopolymers are shown inward Figure 2.
![]() |
Figure 2: Chemical Structures of around biopolymers (a) polylactic acid (b) Poly-(R)-3-hydroxybutyrate (P3HB) (c) polycaprolactone (Source: http://en.wikipedia.org). |
The route of manufacture is equally follows:
Corn → starch → unrefined dextrose → fermentation → lactic acid → monomer production → lactide → polymer (PLA) production → polymer modification → fibre, film, plastic, bottle etc. (3)
Clariant announced the evolution of Biodegradable RENOL®-natur colorant from sustainable, mainly vegetable resources for work amongst these new-age plastics. [19].
Henry Ford offset used soy plastic to create diverse machine parts. Influenza A virus subtype H5N1 novel composite materials has been derived from soy flour too flax resin cross-linked amongst glutaraldehyde, derivable from bio-feedstocks. Materials produced receive got adept mechanical properties too may live used for indoor applications [20]
Recycled Textiles
Because textiles are nearly 100% recyclable, zilch inward textile too clothe manufacture should live wasted. The textile recycling manufacture is 1 of the oldest too most established recycling industries inward the world. Textile recycling materials may live pre-consumer or post consumer (i.e. used garments or articles). The sorting categories of textile recycling past times book is represented past times a pyramid structure, the base of operations of which consists of used cloth marketplace (48%), followed past times conversion to value added novel materials (29%), cutting into wiping too polishing cloths (17%), landfill too incineration for unloosen energy (<7%). The peak of the pyramid is represented past times ‘Diamonds’ (1-2%) which receive got high value for antique lineament or for other reason. [21].
Polyester fibre is 1 of the most non-biodegradable polymers which create environmental problems. Major revolution happened inward 1993 when Wellman Inc. introduced the offset polyester textile fibre made from post consumer PET packaging: Fortrel® EcoSpun®. There are 2 broad types of recycled polyester namely:
If the carpeting fibres are made of polypropylene too they’re held together amongst a polypropylene Licocene back-coating, the production tin live reused precisely past times melting [19].
Greener Dye too auxiliaries
The greener approaches are:
By reacting dextrins amongst obese acids too their derivatives, novel sustainable too biodegradable surfactants receive got been formed. They receive got highly desirable physical properties including depression foaming, adept wetting too whitening ability, equally good equally first-class biodegradability [24].
Queste reported [25] that the researchers inward French Republic too Deutschland receive got jointly developed a novel flat of so-called ‘solvosurfactants’ (which exhibit the properties of both solvent too surfactant too are unremarkably used inward applications such equally coatings too degreasing, equally good equally perfumery too inks) that are derived from glycerol, a renewable stuff from bio diesel.
Greener Preparation too Dyeing
Bio-processing tin precisely live defined equally the application of living organisms too their components to industrial products too processes, which are mainly based on enzymes.
a) Improvement inward the existing dyeing processes
Formaldehyde-free Finishing Agents
The most widely used crosslinking agents inward DP finishes, N-methylol agents or N-methylolamides autumn inward the category of formaldehyde reactants [35]. The release of formaldehyde vapours is a job amongst those agents. It depends on the reactant types, the catalyst types, the status of the treated fabrics, too the additives inward the impregnating bathroom too most importantly the fourth dimension too temperature of cure [36].
Corn → starch → unrefined dextrose → fermentation → lactic acid → monomer production → lactide → polymer (PLA) production → polymer modification → fibre, film, plastic, bottle etc. (3)
Clariant announced the evolution of Biodegradable RENOL®-natur colorant from sustainable, mainly vegetable resources for work amongst these new-age plastics. [19].
Henry Ford offset used soy plastic to create diverse machine parts. Influenza A virus subtype H5N1 novel composite materials has been derived from soy flour too flax resin cross-linked amongst glutaraldehyde, derivable from bio-feedstocks. Materials produced receive got adept mechanical properties too may live used for indoor applications [20]
Recycled Textiles
Because textiles are nearly 100% recyclable, zilch inward textile too clothe manufacture should live wasted. The textile recycling manufacture is 1 of the oldest too most established recycling industries inward the world. Textile recycling materials may live pre-consumer or post consumer (i.e. used garments or articles). The sorting categories of textile recycling past times book is represented past times a pyramid structure, the base of operations of which consists of used cloth marketplace (48%), followed past times conversion to value added novel materials (29%), cutting into wiping too polishing cloths (17%), landfill too incineration for unloosen energy (<7%). The peak of the pyramid is represented past times ‘Diamonds’ (1-2%) which receive got high value for antique lineament or for other reason. [21].
Polyester fibre is 1 of the most non-biodegradable polymers which create environmental problems. Major revolution happened inward 1993 when Wellman Inc. introduced the offset polyester textile fibre made from post consumer PET packaging: Fortrel® EcoSpun®. There are 2 broad types of recycled polyester namely:
- Simply melted too re-extruded into fibres too
- A multi-stage de-polymerisation too re-polymerisation to make ameliorate lineament yarn.
If the carpeting fibres are made of polypropylene too they’re held together amongst a polypropylene Licocene back-coating, the production tin live reused precisely past times melting [19].
Greener Dye too auxiliaries
The greener approaches are:
- Elimination of harmful azo dyestuffs
- Alternative synthesis for eco-friendly products.
- Search for sustainable rootage such equally natural dyes. They, inward general, receive got misfortunate to moderate low-cal fastness. It was found that the natural additives Vitamin C (ascorbic acid) too gallic acid (found inward stomach, tea leaves, oak bark too many other plants) were most effective inward reducing the charge per unit of measurement of fading inward madder, weld too woad dyed cotton fiber [23].
By reacting dextrins amongst obese acids too their derivatives, novel sustainable too biodegradable surfactants receive got been formed. They receive got highly desirable physical properties including depression foaming, adept wetting too whitening ability, equally good equally first-class biodegradability [24].
Queste reported [25] that the researchers inward French Republic too Deutschland receive got jointly developed a novel flat of so-called ‘solvosurfactants’ (which exhibit the properties of both solvent too surfactant too are unremarkably used inward applications such equally coatings too degreasing, equally good equally perfumery too inks) that are derived from glycerol, a renewable stuff from bio diesel.
Greener Preparation too Dyeing
Bio-processing tin precisely live defined equally the application of living organisms too their components to industrial products too processes, which are mainly based on enzymes.
Related:
The application of enzymes inward diverse stages of textile processing may live listed equally follows [26]:
- Desizing: amylase, lipase.
- Scouring: pectinase, cellulase.
- Bleaching: oxidoreductase. xylanase.
- Dyeing: oxidoreductase.
- Finishing: cellulase, oxidoreductase, lipase.
- Composting (biodegradation of textile wastes): cellulase, protease, nylonase, polyesterase.
- Delignification, decolourisation of dyes: laccases [27]
- Purification of cellulose past times extraction past times carbon dioxide too ionic liquids,
- High temperature H2O extraction of lignin,
- Substitution of chlorine bleaching amongst non-polluting oxidants,
- Carbon dioxide-based dry out cleaning.
- Elimination of ozone-depleting chemicals such equally carbon tetrachloride (stain remover).
a) Improvement inward the existing dyeing processes
- Optimise processes (to cut down fourth dimension too unloosen energy consumption)
- Reduce consumption of water, electrical power, steam consumption
- Optimise dye/chemical costs
- Eliminate reprocessing too shade correction
- Sulphur dyeing: commutation of hazardous sodium sulphide amongst sustainable, nontoxic, biodegradable, cost-effective reducing sugars [28].
- Reactive dyeing: handling of cellulose amongst cationic, nucleophilic polymers enables dyeing at neutral pH without electrolyte improver - 3-chloro-2-hydroxypropyl-trimethylammonium chloride (CHTAC) [29], Copolymer of diallyldimethylammonium chloride too 3-aminoprop-1-ene too copolymer of 4-vinylpyridine quaternised amongst 1-amino-2-chloroethane [30].
- In chemical-free denim processing [31], Light Amplification by Stimulated Emission of Radiation engineering is used to burn downwardly away the surface of the dyed denim stuff or a brace of jeans on a mannequin to replicate an authentic worn look. The Light Amplification by Stimulated Emission of Radiation organisation is really quick too a brace of jeans tin bring equally piddling equally xv seconds to process.
- Right-First-Time dyeing: It is also termed equally ‘no addition’ dyeing or ‘blind dyeing’. Elimination of the inspection stage made a pregnant saving [32]. Twenty factors which must live monitored or controlled to attain RFT processing inward the dyeing procedure receive got been identified [33].
- About 90% dye fixation on batchwise cellulose dyeing amongst polyfunctional dyes.
- Cold pad-batch dyeing, rapid dyeing techniques too ameliorate machine design.
- Economic continuous dyeing methods.
- Supercritical carbon dioxide dyeing (Figure 3)
![]() |
Figure 3. Supercritical State of CO2 |
The most widely used crosslinking agents inward DP finishes, N-methylol agents or N-methylolamides autumn inward the category of formaldehyde reactants [35]. The release of formaldehyde vapours is a job amongst those agents. It depends on the reactant types, the catalyst types, the status of the treated fabrics, too the additives inward the impregnating bathroom too most importantly the fourth dimension too temperature of cure [36].
The Occupational Safety too Health Administration (OSHA) receive got laid the upper bound for formaldehyde inward air at 0.75 parts per 1000000 averaged over an eight-hour piece of work shift [37]. Formaldehyde is a carcinogen to animals [36]. Some formaldehyde-free DP finishes are:
An interesting evolution inward the plain of flame retardancy is the work of polymer nanocomposites equally a substitute of toxic brominated flame retardants (BFR). Nanocomposites may live described equally two-phase materials, consisting of a dispersion of appropriate filler (on a nanometre scale) through a polymer matrix. In the instance of polymer-layered silicate (clay) nanocomposites, exclusively a really pocket-size amount of filler (2-10 weight-%) is required for the stuff to live flame-retardant [39].
Automation
Pollution reduction is possible through automation inward textile dyeing too printing. The steps are:
For improvement inward the quality: steps (a) too (c) must live adopted
For man-power savings: steps (a) too (b) are to live followed
For terms reduction: stair (d) is to live adopted.
For ameliorate customers’ service (RFT production, quick reply too just-on-time delivery): steps. (a) to (e) (full automation).
- Cyclic improver of glyoxal amongst NN/dimethyl urea, namely DHDMI (1,3 dimethyl-4,5-dihydroxyethyleneurea)
- Polycarboxylic acids (PCA) - their primary drawback is loss of tensile clitoris due to acid-catalysed cellulose chain cleavage. The most of import PCA reactants are butanetetracarboxylic acid (BTCA) too citric acid (CA) [38]. BTCA, inward the presence of sodium hypophosphite, provides the same flat of durable press performance equally conventional DMDHEU reactant, but it is quite costly [37].
An interesting evolution inward the plain of flame retardancy is the work of polymer nanocomposites equally a substitute of toxic brominated flame retardants (BFR). Nanocomposites may live described equally two-phase materials, consisting of a dispersion of appropriate filler (on a nanometre scale) through a polymer matrix. In the instance of polymer-layered silicate (clay) nanocomposites, exclusively a really pocket-size amount of filler (2-10 weight-%) is required for the stuff to live flame-retardant [39].
Automation
Pollution reduction is possible through automation inward textile dyeing too printing. The steps are:
- Process command - 10-30% saving inward H2O too unloosen energy equally good equally 5-15% saving inward dyes too chemicals.
- Auto-dispensing - 5-10% savings inward dyes, pigments too chemicals.
- Computer-controlled weighing too stock-taking - 10-15% savings inward dyes, pigments too chemicals.
- Colour mensuration too matching - pregnant improvement inward lineament too 30-40% savings of dyes too pigments.
- Central estimator (network), computerised management system.
For improvement inward the quality: steps (a) too (c) must live adopted
For man-power savings: steps (a) too (b) are to live followed
For terms reduction: stair (d) is to live adopted.
For ameliorate customers’ service (RFT production, quick reply too just-on-time delivery): steps. (a) to (e) (full automation).
Eco-legislation
REACH [40] is a novel European Community Regulation on chemicals too their security use. It is a novel regulatory framework proposed past times the EC on Oct 29, 2003. It is a single, coherent organisation for novel too existing chemicals amongst the next iii novel elements:
Green Chemistry provides a technical solution to many environmental problems. It is effective due to blueprint stage efforts, starting at the molecular flat lets 1 to blueprint out the hazardous properties too to blueprint inward environmentally appropriate features.
The 21st century philosophy for textile dyeing is follows:
The textile industry is 1 of the highly revenue generating industries inward Bharat too many other developing countries. Pollution created past times textile industries is a large job for them. Modern technologies similar microbial decolorization too degradation are piece of cake existence adopted for the handling of polluted water. There is an increasing involve of exploring biodiversity for natural dyes too developing eco-friendly methodology for synthetic dyes too dyeing. All these require to a greater extent than funding inward the R&D of respective fields too greater interaction too coordination betwixt industry, academia, too authorities [43].
References
REACH [40] is a novel European Community Regulation on chemicals too their security use. It is a novel regulatory framework proposed past times the EC on Oct 29, 2003. It is a single, coherent organisation for novel too existing chemicals amongst the next iii novel elements:
- Registration (30,000 substances traded inward EU; 100,000 on EINECS)
- Evaluation (5,000 substances)
- Authorisation (1,350 substances) of Chemical Substances
- To improve the protection of human wellness too the surroundings
- To increment the competitiveness of the European Union chemicals manufacture
- To increment transparency
- To attain integration amongst global efforts
- To adapt amongst European Union international obligations nether the WTO
- To promote non-animal testing.
Green Chemistry provides a technical solution to many environmental problems. It is effective due to blueprint stage efforts, starting at the molecular flat lets 1 to blueprint out the hazardous properties too to blueprint inward environmentally appropriate features.
The 21st century philosophy for textile dyeing is follows:
- Minimum human/operator intervention,
- Process steps optimised for utility consumption,
- Decisions made strategically non on a daily routine basis,
- Processes devised too selected to make the right shade too lineament equally an expectation non precisely an intention,
- Digital shade passing too color communication,
- Profits are made past times doing it right - non precisely past times doing it cheaply [41].
- Become carbon neutral,
- Send no waste materials to landfill,
- Develop sustainable sourcing routes,
- Set novel standards inward ethical trading,
- Help customers too employees to alive a healthier lifestyle.
The textile industry is 1 of the highly revenue generating industries inward Bharat too many other developing countries. Pollution created past times textile industries is a large job for them. Modern technologies similar microbial decolorization too degradation are piece of cake existence adopted for the handling of polluted water. There is an increasing involve of exploring biodiversity for natural dyes too developing eco-friendly methodology for synthetic dyes too dyeing. All these require to a greater extent than funding inward the R&D of respective fields too greater interaction too coordination betwixt industry, academia, too authorities [43].
References
- P. Anastas too J. C. Warner, Green Chemistry, Theory too Practice, Oxford University Press, New York, 1998.
- www.epa.gov/ greenchemistry/
- M. Kidwai, Green chemical scientific discipline inward India, Pure Appl. Chem., Vol. 73, No. 8, pp. 1261–1263 (2001).
- Graham J. Hutchings, Green Chemistry has a Golden Future, Europacat7, (August) Cardiff University, UK) (2005).
- Martyn Poliakoff too Pete Licence, Nature, 450 (6) Dec (2007).
- R. A. Sheldon, (2005). Green Chem., 7, 267 (2005).
- D. C. Rideout too R. Breslow, J. Am. Chem. Soc., 102, 7816 (1980).
- Chao-Jun Li, Green Chem., 10, 151–152, (2008). DOI: 10.1039/b800137p.
- Chao-Jun Li, Canadian Chemical News, Apr , (2004).
- Ryoji Noyori, Chemical Communications (Royal Society of Chemistry) (14), 1807 – 1811 (2005).
- E. Bach, E Cleve, too E. Schollmeyer, Rev. Prog.Color. 32, 88 (2002).
- M. van der Kraan, Process too Equipment Development for Textile Dyeing inward Supercritical Carbon Dioxide, Ph. D thesis at Technische Universiteit, Delft too J. Supercrit. Fluids 34, 99 (2005).
- Z Khatri too Khan Muhammad Brohi, Environmental Friendly Textiles - a route to sustainability, www.Knol.google.com.
- H. Zollinger, Color Chemistry, Synthesis, Properties of Organic Dyes too Pigments, 2nd ed., VCH Publishers, New York, 92 (1987).
- B.M. Müller, Rev. Prog. Coloration, 22, 14-21 (1992).
- A.K. Roy Choudhury Textile Preparation too Dyeing, Science Publishers (Enfield, NH: USA), 2006.
- W Albrecht, M Reintjes too B Wulfhorst, Chem. Fibers Int., 47, 298 (1997)
- P White, M Hayhurst, J Taylor too Influenza A virus subtype H5N1 Slater, Biodegradable too Sustainable Fibres. (Ed.) R south Blackburn (Cambridge: Woodhead), 157, 2005.
- Walking the talk: Clariant products provide ‘green’ chemical scientific discipline successes, News Release, www.clariant.com, August xix (2008).
- S. Chabba et al., Green Chemistry, 7, 576 (2005).
- J. M. Hawley Textile recycling: Influenza A virus subtype H5N1 organisation perspective, inward Recycling inward Textiles, Y Yong (eds), (Cambridge: Woodhead), (2006).
- Dyeing Recycled Pet, www.ecotextile.com.
- D. Cristea & G. Vilarem, Dyes too Pigments, 71, 39 (2006).
- H. J. Wang too K-M. Chen, J. Applied Polymer Science, 98, 711 (2005).
- S. Queste et al., Green Chem., 8, 822 (2006).
- I. Holmes. Colourage Annual, 41-56 (1998)
- K. Li et al., Appl. Environ. Microbiol. 65, 2654–2660, (1999).
- Richard S. Blackburn too Anna Harvey, Environ. Sci. Technol., 38 (14), pp 4034–4039 (2004).
- M Hashem, P Hauser too B Smith, Text. Res. J., 73 , 762 (2003).
- Richard S. Blackburn, Stephen M. Burkinshaw, Journal of Applied Polymer Science, Vol. 89, 1026–1031 (2003).
- Chemical-free denim processing, www.ecotextile.com.
- J Park too J Shore Color. Tech., 125, 133-140 (2009).
- Park too J Shore, Practical Dyeing (Bradford: SDC), 2004.
- T.L. Dawson, Color. Tech., 124, 67-78 (2008).
- H. Peterson, Review of Progress inward Coloration too Related Topics, 17, 7-22 (1987).
- T. F. Cooke & H. D. Weigmann, Textile Chemist too Colorist, 14, 100-106.& 136-144 (1982).
- B. A. K. Andrews, Textile Chemist too Colorist, 22, 63-67. (1990).
- C. M.Welch, Textile Research Journal, 58, 480-486 (1988).
- www.eupen.com/highlights/publications.html.
- www.fibre2fashion.com.
- A C Welham, www.dyehousedoctor.com, Textile Dyeing inward the Age of Aquarius.
- Mark Sumner, (2009). Plan Influenza A virus subtype H5N1 & Eco Dyehouses, Part I, (Bradford: Society of Dyers too Colourists).
- A.K. Roy Choudhury, Green Chemistry too the Textile industry, Textile Progress, Volume 45, Issue 1, 2013 (Textile Institute, UK). http://www.tandfonline.com/doi/full/10.1080/00405167.2013.807601