Now You Know Waterproof Breathable Fabrics: Product Modification and Recent Developments (Part-1)
Friday, 8 March 2019
Edit
Waterproof Breathable Fabrics: Product Modification and Recent Developments (Part-1)
Shailja Sharma
M. Tech. Scholar
Department of Textile Technology,
NIT Jalandhar, India
Cell: +91- 8872-431933
Email: shailjadrs@gmail.com
M. Tech. Scholar
Department of Textile Technology,
NIT Jalandhar, India
Cell: +91- 8872-431933
Email: shailjadrs@gmail.com
Abstract:
The article is about the developments which took place in the recent times in the field of waterproof breathable fabrics. Waterproof Breathable fabrics shows the contradictory property of waterproofness as well as it allows the moist vapours from body to diffuse to the environment. There is a large variety of waterproof breathable fabrics which includes densely woven fabrics, micro porous and hydrophilic membranes and coatings, their combinations etc. Multilayered breathable fabrics are also being developed in recent times to enhance the functional characteristic of the fabric. The area has experienced a huge growth in the past few years as the waterproof breathable fabrics proved very effective in a number of fields such as active sportswear, mountaineering, military and some of the protective clothing also. Some of the leading manufactures such as ASF Group, MarmotTM, PatagoniaTM, and The North FaceTM etc are working in this field to develop new products with the changing scenario.
Keywords: Breathability, bi-component laminates, ceramic, DWR, TS-PU, Temperature-Sensitive Copolymer, HPMC, Biomimetics, INOTEK Fibres.
1. Introduction:
Breathability as explained in terms of fabric is different as understood in general which means the material should be actively ventilated [2]. Waterproof Breathable fabric should allow the water in vapour form to diffuse through it but at the same time it should restrict the entry of water in liquid form such as rain etc and with this contradictory functional requirement the fabric should comfortable enough to the wearer when converted into a garment. Waterproof Breathable fabric gives protection against weather like wind, rain and loss of body heat [1] [14]. The breathable fabrics find its application in the field of sportswear; (where the basic requirement is thermal, sensorial and body movement comfort of fabric and protection from adverse weather) [4], hygiene, agriculture, protective clothing, and construction industries etc [2].
There are different categories of waterproof breathable fabrics as listed below [1] [3];
Classification based on conventional methods of production is:
2. Scope of Development:
Scope for development in any engineering field is always limitless. Research and Development is an easy task if the problem is well known. Problems can be cost effective production, alternative method of production, better functional characteristic in the product, economic and environmental friendly solution etc. As far as waterproof breathable Fabrics are concerned the formulation and application of micro-porous and hydrophilic membranes and coatings have been well researched in different fields of applications. Smart breathable fabrics and fabric based of biomimetics, which has recently gained popularity, has started to show a great potential [1]. The use of polyester microfilaments in densely woven structure has also proved its worth in waterproof breathability, thermal insulation and wind proof character of fabric [5].
A great scope for development also arises with the development of new ideas in the field. The leading manufacturers in the field has developed new product range such as THERMOBALL by The North Face which can offer the light weight, loft, warmth and compressibility of down [10], NanoPro and NanoPro Membrain by Marmot [7] also some other names are there such as Patagonia [9], ASF Group [8] etc. Some of the recent developments which were witnessed in past few years are discussed in the next section.
3. Recent Developments:
3.1 Modification in the existing products and processes
ii. Use of Ceramic in Coatings
Polyurethane (PU) is used conventionally as micro-porous coating on the fabric. In recent times, Ceramic is being used in coating which provide many more holes to transport the perspiration vapours away from the body by improving moisture vapour transmission of the fabric. Due to the addition of ceramic in the coatings finer holes are being formed and it adds about 20% more waterproof protection [8].
iii. Super Shed™ DWR Application[8]
This newly developed DWR technology uses a water repellent agent and a collateral process technology that densely aligns water repellent groups and bonding them firmly to the nylon fabric. This Technology was rated 80 using the water repellency spray test method even after over 100 repeated washing. Generally the DWR wears off with time are re-treatment is recommended when necessary. With this improved technology the treatment stays for a longer period of time in the fabric.
iv. Reduced Pore Size
Keywords: Breathability, bi-component laminates, ceramic, DWR, TS-PU, Temperature-Sensitive Copolymer, HPMC, Biomimetics, INOTEK Fibres.
1. Introduction:
Breathability as explained in terms of fabric is different as understood in general which means the material should be actively ventilated [2]. Waterproof Breathable fabric should allow the water in vapour form to diffuse through it but at the same time it should restrict the entry of water in liquid form such as rain etc and with this contradictory functional requirement the fabric should comfortable enough to the wearer when converted into a garment. Waterproof Breathable fabric gives protection against weather like wind, rain and loss of body heat [1] [14]. The breathable fabrics find its application in the field of sportswear; (where the basic requirement is thermal, sensorial and body movement comfort of fabric and protection from adverse weather) [4], hygiene, agriculture, protective clothing, and construction industries etc [2].
![]() |
Waterproof breathable fabrics |
Classification based on conventional methods of production is:
- Densely woven fabrics
- Micro-porous and Hydrophilic membranes
- Micro-porous and Hydrophilic coating
- Combination of micro-porous and hydrophilic membranes and coating
- Retroreflective microbeads
- Smart breathable fabrics
- Fabrics based on biomimetics
2. Scope of Development:
Scope for development in any engineering field is always limitless. Research and Development is an easy task if the problem is well known. Problems can be cost effective production, alternative method of production, better functional characteristic in the product, economic and environmental friendly solution etc. As far as waterproof breathable Fabrics are concerned the formulation and application of micro-porous and hydrophilic membranes and coatings have been well researched in different fields of applications. Smart breathable fabrics and fabric based of biomimetics, which has recently gained popularity, has started to show a great potential [1]. The use of polyester microfilaments in densely woven structure has also proved its worth in waterproof breathability, thermal insulation and wind proof character of fabric [5].
A great scope for development also arises with the development of new ideas in the field. The leading manufacturers in the field has developed new product range such as THERMOBALL by The North Face which can offer the light weight, loft, warmth and compressibility of down [10], NanoPro and NanoPro Membrain by Marmot [7] also some other names are there such as Patagonia [9], ASF Group [8] etc. Some of the recent developments which were witnessed in past few years are discussed in the next section.
3. Recent Developments:
3.1 Modification in the existing products and processes
Related:
i. Bi-component Micro-porous and Hydrophilic Laminates
Using two components together is always beneficial as the advantages of both components can be utilized in one system that is why; Bi-component waterproof breathable fabrics are gaining interest in the market these days. This is because their combined system is proved effective in diffusion of perspiration vapours as well as condensed liquid perspiration. Hydrophilic systems do not transport perspiration vapour, but only the liquid perspiration formed when the vapour condenses whereas Micro-porous hydrophobic systems transport vapour, but do not transport condensed perspiration [8]. By using a Bi-Component System that uses both hydrophilic and hydrophobic micro-porous elements most effective waterproof breathable system can be made. In this system Micro-porous PTFE membrane and hydrophilic Polyurethane (PU) are used together as a bi-component. The micro-pores of the PTFE are filled with hydrophilic PU. There is some evidence that an air layer exists between the PTFE and PU that provides insulation, increasing the temperature differential between the inside and outside of the fabric, and this can reduce condensation. The durability of this bi-component can be only due to use of high hydrophilic PU else chances of damage are more. This is also called Modern Gore-Tex and it is impermeable to air [15]. 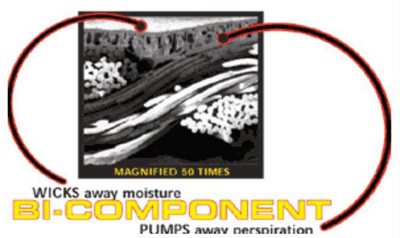
Polyurethane (PU) is used conventionally as micro-porous coating on the fabric. In recent times, Ceramic is being used in coating which provide many more holes to transport the perspiration vapours away from the body by improving moisture vapour transmission of the fabric. Due to the addition of ceramic in the coatings finer holes are being formed and it adds about 20% more waterproof protection [8].
iii. Super Shed™ DWR Application[8]
This newly developed DWR technology uses a water repellent agent and a collateral process technology that densely aligns water repellent groups and bonding them firmly to the nylon fabric. This Technology was rated 80 using the water repellency spray test method even after over 100 repeated washing. Generally the DWR wears off with time are re-treatment is recommended when necessary. With this improved technology the treatment stays for a longer period of time in the fabric.
![]() |
Comparison between SuperShedTM DWR and Conventional DWR technology |
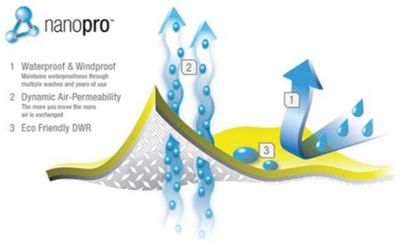
Earlier the micro-porous membrane pore size was 2-3 micrometers which is reduced by 30% in this new technology which is recently launched by one of the leading manufacturers (Marmot) of waterproof breathable fabrics and it is named as NanoPro™. These very small pores which are densely packed improve the waterproofness and breathability of the fabric. This pore structure is also air permeable allowing for dynamic air exchange. Dynamic Air Permeability allows for air exchange to more quickly shed moisture vapour without compromising waterproof performance or wind protection.[9].
![]() |
Sumber http://textilelearner.blogspot.com