Now You Know Fabric Defects and Their Causes
Friday, 8 March 2019
Edit
Fabric Defects and Their Causes
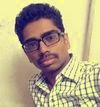
Bhavdip Paldiya
Dept. of Textile Technology
Sarvajanik College of Engineering & Technology, Surat, India
Cell: +91 9662020909
Email: bhavdipk9009@gmail.com
Introduction:
Fabric defects can have various reasons caused by raw material, the spinning process, weaving, knitting and dying. Fabric defects are responsible for major defects found by the garment industry. Due to the increasing demand for quality fabrics, high quality requirements are today greater since customer has become more aware of “Non-quality” problems. In this article i have discussed different types of faults and their causes and remedies.
Related:
Sr. no. | Defect Name | Appearance | Cause | Responsibility of weaver |
1 | Crack | Too few picks per inch in a certain area. | A. Bad start up procedure by weaver B. let of or take up worn or broken C. improper tension on warp D. weft feeler problem | A. more care required while pick finding, B. stop loom, call supervisor or mechanic |
2 | Float | Distortion of in weft direction generally accompanies with warp break | A. fluff or knot behind the reed . B. spare end weaving in C. knot with long tails. D. warp stop motion not working not working | Remove the cause |
3 | Wrong Drawing | Irregular pattern warp way in the cloth. | Weaver incorrectly drawing in the healds. | Correct the draw |
4 | Leno Problem | Leno end not holding correctly | A. wrong drawing in leno device B. build up of dirt or fly. C. wrong tension on ends D. faulty leno device. | A. correct the draw B. clean off C. adjust tension D. call mechanic |
5 | Missing End | Warp line, thin gap in warp direction | A. fluff in drop wires. B. warp stop motion not working. C. missing drop wire . D. electrical fault. E. incorrect setting of warp stop motion. | A. blow the air regularly. B. inform mechanic supervisor. C. replace it. d. inform super visor. E. inform supervisor. |
6 | Design Mistake | Incorrect design | A. wrong design put in microprocessor | Stop loom and inform supervisor |
7 | Wrong Weft | In correct weft | In correct count or colour of weft | Ensure correct use of weft and always check weft as per loom card. |
8 | Slough Off | loose coils of weft in the fabric. | Bad cones, or incorrect tension. | Replace the cone or inform supervisor. |
9 | Pull Terry | Pile end are pulled/cut across the fabric width | In foreign bodies come in contact with needle ,needle could be damaged or take up motion problem . | Inform supervisor /mechanic |
10 | Reverse Terry | Pile formation in plain portion of cloth | Pile/ground beam tension problem | Inform supervisor/mechanic. |
11 | Starting Mark | Think or thin places at the start up the loom . | Incorrect loom setting | Call mechanic/ inform supervisor |
12 | Defective Selvedge | No fringes from cutters cloth may be cut. | Wrong position selvage 0cutters | Replace the end until end is clean. |
13 | Defective Border | Warp line | Reed dent s bent or damaged | Flag fixer |
14 | Oil Stain | Warp line corresponding to the temple | Damaged or broken temple rings. | Flag fixer |
15 | Shade Variation | Selvage ends weaving incorrectly | Weaver incorrectly drawing in selvage ands | Stop loom and correct |
16 | Dobby Held Problem | Heavy line warp way | Two ends in the same heddle | Remove extra end |
17 | Reed Mark | Visible line warp way in the cloth | A. weaver error B. portion of yarn with incorrect twist. C. fault in warping or drawing in. | A. weaver fault B. remove and mark the end. C. Flag fixer |
18 | Uneven Pile Height | Visible line filling way in the cloth | A. broken filling not completely removed B. pick finding incorrect C. faulty filling detector. | A. weaver fault B. weaver fault C. Flag fixer |
19 | Emery Mark | Thick line across cloth | A. Incorrect pike finding B. reserve cone caught and running | A. weaver fault B. weaver fault; correct |
20 | Damage Mark | Filling bar | A. wrong cone creeled B. mixed yarn in spinning or winding | A. weaver fault B. stop loom, flag supervisor |
Sumber http://textilelearner.blogspot.com