Now You Know Comprehensive Study on Loom Timing
Sunday, 3 February 2019
Edit
Comprehensive Study on Loom Timing
Raju Tex
Production Executive, B.J.Group
Chittagong Textile Engineering College
Facebook: https://www.facebook.com/ERZRAZU
Production Executive, B.J.Group
Chittagong Textile Engineering College
Facebook: https://www.facebook.com/ERZRAZU
Loom Timing
Loom timing is defined as relative chronological sequences of various primary and secondary motions are expressed in terms of degree of crank shaft rotation. The loom timing is presented by a diagram termed as “Loom Timing Diagram”. The diagram depicts the start and end of each primary event of different weaving motions. The start and end of events are influenced by loom type, fabric width and fabric type. The loom timing is shown in the Figure.
![]() |
Loom Timing Diagram |
Some others are related to it indirectly. For example. the timing of the weft break stop motion is related to the flight of the weft carrier, which is governed by the position of the reed. The timings on the weaving machine are stated in relation to the angular position of the crankshaft (main shaft) which operates the sley.
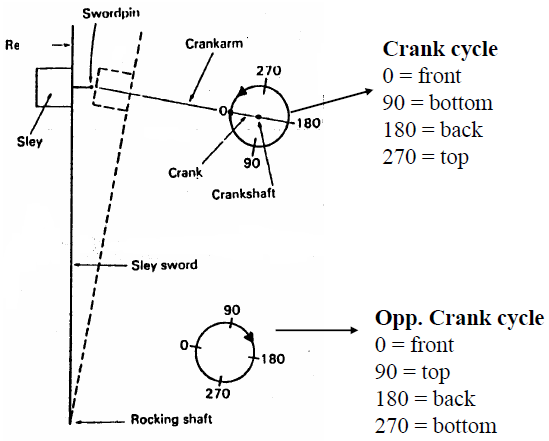
The crank circle is graduated in degrees from this point in the direction of rotation of the crankshaft. Any timing can be stated in degrees, as, for example, ‘healds level at 3000’
Related:
Looms are provided with a graduated disc on the crankshaft and a fixed pointer to make settings in relation to the angular position of the crankshaft. With the reed in its most forward position, the disc is adjusted so that the pointer is opposite to 00 on the graduated scale. The loom may then be turned to any desired position manually, the disc turning with it and the pointer remaining vertical and indicating the angular position of the crank shaft. In modern looms with microprocessors, the main shaft position is displayed on a screen, but the setting principle remains same.
Sumber http://textilelearner.blogspot.com