Yaa An Overview Of Roller Carte Du Jour Inward Carding
Friday, 21 December 2018
Edit
Roller Card In Carding
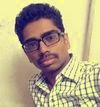
Bhavdip Paldiya
Dept. of Textile Technology
Sarvajanik College of Engineering & Technology, Surat, Bharat
Cell: +91 9662020909
Email: bhavdipk9009@gmail.com
CARDING
Carding is a mechanical procedure that disentangles, cleans together with intermixes fibers to arrive at a continuous spider web or sliver suitable for subsequent processing. This is achieved past times passing the fibers betwixt differentially moving surfaces covered amongst menu clothing. It breaks upwards locks together with unorganized clumps of fibre together with so aligns the private fibres to hold out parallel amongst each other. In preparing wool fiber for spinning, carding is the pace that comes afterwards teasing.
The proverbs of the experts “The Card is the pump of the Spinning Mill” together with “Well Carded is one-half spun” demonstrate the immense significance of carding for concluding number of the spinning operation.
Carding procedure
The opened together with blended fibres so undergo carding process. The functions of the carding procedure are
- Individualization of fiber tufts to almost unmarried fiber
- Mixing of fibers to average out variations inwards fiber characteristics
- Forming a homogenous spider web of uniform weight per unit of measurement expanse
1. FOR NON-WOVEN
In the example of brusk staple system, the revolving apartment menu is used, but for long staple scheme the roller top menu is used. As the dry-laid procedure by together with large utilizes the long staple fibres the roller top menu is oftentimes seen to hold out used inwards the nonwoven industry.Figure 1 displays the diagram of a roller top card. Though this menu is like to the revolving apartment menu inwards its basic features, but it differs from the apartment top menu inwards several respects, including the fact that their primary carding fields are designed differently. The flats are replaced past times pairs of rollers, equally shown inwards Figure 1;
![]() |
Figure 1 |
The basic principles of carding procedure are lying inwards carding activeness together with stripping action. The disentangling of fibres is done past times carding activeness together with the transfer of fibres is done past times stripping action. In fellowship to realize the carding activeness betwixt ii surfaces, the wire points of the ii surfaces must receive got contrary inclination, but inwards fellowship to realize the stripping activeness betwixt ii surfaces, the wire points of the ii surfaces must receive got the same inclination. This is illustrated inwards Figure 2.
![]() |
Figure 2 |
Besides the carding together with stripping action, the feeding, doffing, together with spider web forming are also of import together with many interesting developments receive got been taken house inwards these regions so far,
![]() |
FIGURE 3 |
The dish feed organisation results inwards relatively harsh handling to fibers, but the roller feed organisation results inwards relatively mildtreatment to fibers. The seat of clearer roller depends on whether the taker-in is down-striking or up-striking.
Also, at that spot are advancements going on inwards the doffing region. The double doffer scheme (IN BELOW FIG 4) tends to increase fiber transfer from cylinder to doffers, thereby increase production.
![]() |
FIGURE 4 |
![]() |
FIGURE 5 |
The spider web formation part is also of involvement for R&D. The oscillation frequency of the doffer comb is technologically limited, which inwards plough limits doffer speed, so production. High production cards run doffer at 25-40 rpm where the doffer comb can’t hold out used for stripping, but pull off rollers whose surface speed is slightly higher than that of doffer tin hold out used to withdraw spider web through stripping action. More advanced doffing scheme utilizes a pull off roller, perforated apron together with suction scheme to command spider web transfer to the apron
Productivity of older roller cards is near 30-50 kg/hour at the width of 1.5 2m. Nowadays, the roller cards of performance upwards to 1000kg/hour inwards width 2 3.5m are delivered. Flat carding machines are commonly 1m broad together with procedure near five 50kg/hour.
Garnett
Garnetts are like to roller-top cards. R.L. Street has described the garnett equally "a grouping of rolls placed inwards an fellowship that allows a given wire configuration, along amongst surely speed relationships, to level, transport, comb together with interlock fibers to a grade that a spider web is formed."[2] Garnetts are by together with large used to procedure waddings together with for making pads for automobile together with bedding industries. It delivers a to a greater extent than random spider web than a card. Most webs from garnetts are layered past times crosslapping to construct upwards the desired finished nonwoven weight.
2. FOR WOOL CARDING
Worsted yarns are made from virgin wool fibres. The blending procedure is followed past times scouring together with drying, to rid the wool of its fat, suint together with dirt.The clean, moist wool theb passes through 1 of ii processes; it is either “prepared” or “carded”. The selection is determined mainly hold out the length; if this is longer than 7 inches it is prepared, if shorter it is carded.
![]() |
Wool Carding |
The carding actions falls into 3 categories:
- Point to point, a fraction of fibres beingness retained past times both surfaces (worker/swift,doffer/swift)
- Point to back, all fibres removed from 1 surface to closed to other (worker/stripper,stripper/swift)
- Back to back, fibres raised from 1 surface past times closed to other (fancy/swift)
![]() |
Carding actions |
SOME SPECIFICATION OF WORSTED ROLLER CARD
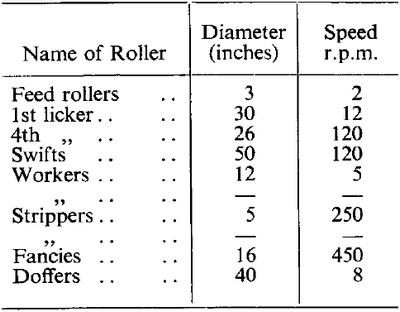
SOME MANUFACTURER OF ROLLER CARD:-
- TRĂśTZSCHLER NONWOVENS;
- DILOSPINNBAU;
- GARNETT CARD CLOTHING;
- RAMELLA PIETRO;
- BEKAERT NON-WOVEN CARD CLOTHING;
- DEECO MECHATRON MKTG. PVT. LTD.;
- AUTEFA.