Now You Know Method to Control Fabric / Piece Goods Quality
Sunday 3 February 2019
Edit
Method to Control Fabric / Piece Goods Quality
Smallest part of fabric is known as fiber. Yarn for textile is made through the fiber but textile can be made directly from the fiber without even converting it into the yarn. Felt is one of the examples of non woven material, directly made from the fiber. Textile can be made through man made material and material from nature. The world of textile is enormous and in this section we would discuss about the procedure and method of quality control of textile / fabric.
If we define the steps of fabric from birth till end use (life cycle) then it will be like following:
- Design thought : Conceptual development
- Development: Development of conceptual thought in reality as samples.
- Lab dip approval : First approval for the mass production
- Bulk start and approval: After the lab dip approval manufacturing of bulk lot fabric starts and initial lot should be approved.
- Bulk ready: fabric ready for the mass manufacturing of apparel.
- Bulk consumption: Apparel manufactured.
- End use: Final retailing of apparel
INSPECTION PROCEDURE:
There are many systems for the quality audit of fabric / piece goods.
Most familiar system is 10 point system, Dallas system and 4 point system.
1. 10 point system: Method of point calculation
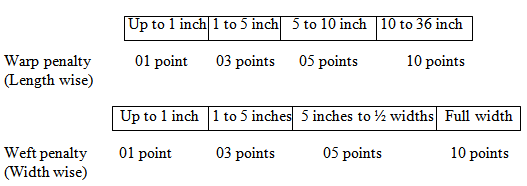
In this system points should not exceed the total yardage of fabric roll.
Suppose penalty point of a roll is 50 and total yardage is 50 than it is ok and will be considered as first quality. If, penalty points exceeds than the total yardage such as 50 penalty points out of 50 meter roll than it should be considered as second quality.
2. Dallas System: This system was introduced by “Dallas apparel manufacturing association” and it was only for knits manufacturing industry hence it is not the complete system which could be followed.
3. Four point system: This is the most familiar and widely accepted system. At least 10% peace goods (Fabric) should be inspected under this system. Selection of rolls should be of each color and randomly selected. Following is the method of point’s calculation in this system.

The size of defect decides the penalty points. In one linear yard the maximum of 4 points should be charged. In fabric only major defects should be taken into consideration such as hole, slub, contaminated yarn, missing yarns, needle line in knit fabric, miss print, color defect, color variations etc because these defects are prominently visible in ready garment. Minor defects which are repairable normally not considered defect in fabric such as soiled yarn, fly, knots etc
HOW TO INSPECT, ACCEPT AND REJECT YOUR FABRIC
Normally 40 points are acceptable in per 100 yards.
Example:

The size of defect decides the penalty points. In one linear yard the maximum of 4 points should be charged. In fabric only major defects should be taken into consideration such as hole, slub, contaminated yarn, missing yarns, needle line in knit fabric, miss print, color defect, color variations etc because these defects are prominently visible in ready garment. Minor defects which are repairable normally not considered defect in fabric such as soiled yarn, fly, knots etc
HOW TO INSPECT, ACCEPT AND REJECT YOUR FABRIC
Normally 40 points are acceptable in per 100 yards.
Example:
- Suppose one consignment has come of 3000 yards.
- As per rule 10 % piece goods are inspected.
- Out of 300 yards total penalty points 205 reported.
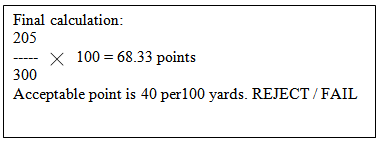
However one may analyze the individual roll wise rejection.
Example: Inspected 10 rolls. Found 3 rejected.
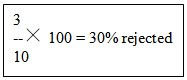
In this case 100% inspection would be required for separation of good and bad roll of fabric.
It is totally depend on factory management for the inspection % of goods. The main criteria is ultimate goods should be defect free.
Among all three, 4 point system is the most effective system.
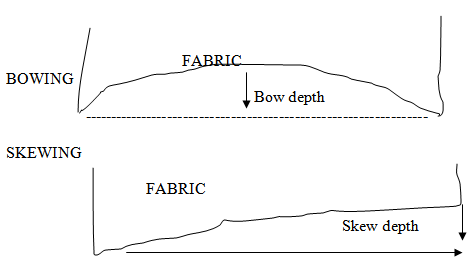
Defect points calculation:
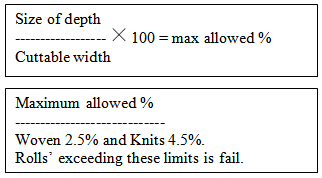
Some important points to be taken care of:
- On purchase order factory may write many of the basic required quality points for supplier, which need to be followed.
- Suppliers own inspection report should be available before dispatch of fabric.
- While inspection, approved fabric must be there for the comparison with bulk lot.
- Following should be checked while doing the fab.inspection: Color shade checking, Side to side salvage color, side to middle color, beginning and end fabric etc. Inspect on machine with appropriate light and speed to detect the defects. Weight, yarn count, Bowing, skewing, odour, softness of fabric, shrinkage of yarn and fabric etc.
- Color wise defect identification and major defect should be with red sticker and thread should be knotted on the salvage for easily identifying the defects when representative come.
- Yard quantity, face and reverse side must be identified on sticker of roll. Colored sticker used for reject and ok fabric roll. Roll sticker should have at least following information: Roll number, Roll length, roll weight (if knits), dye/ print/ color shade lot, supplier name, fabric composition and description, cuttable width, defect points etc.
- Writing record is required for quality inspection in simple and easy to understand format. Minimum 6 months past record required in audit as according to international norms.
- All the fabric should be on pallets or properly placed in wracks with proper identification.
- Classification of defect / sample identified on display board for better understanding. Such as satin should be specially inspected for yarn pull, crape for density of crape and required width, printed fabric for miss print etc
1. Restricted chemicals: This is very important and emerging area of concern. Supplier of fabric, dying, printing etc must have awareness regarding these international norms.
2. Color shade control
2A. Color continuity record:
a. Continuity records required to control the color and shades. Small swatches from every fabric roll taken out and matched with approved shade in unwashed and after wash condition. Record must be kept with all the information on top of every swatch. Shade should be checked in full width
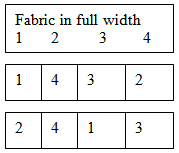
Color shade should be compare between swatches and especially on the edges.
b. From every roll at least 10 by 10 cm swatch should cut and see the continuity of color.
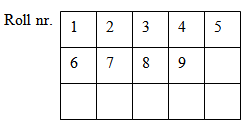
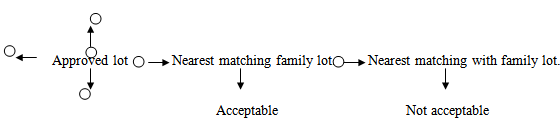
- Fabric information given by the supplier.
- Based on the supplier information fabric performance test
- Garment test
![]() |
Click on image for large size |
EQUIPMENTS REQUIRED IN FABRIC DEPARTMENT AND THEIR MINIMUM REQUIRED SPECIFICATION.
- Fabric inspection machine: It should be motorized with variable speed control along with meter / yard counter and with minimum 1000 lux lighting.
- Light box: Installation of light box should be in dark room and it should have day light, uv light, TL83, TL84 etc for color shade matching with approved shade in different lights. Lights must be changed every year and maintenance records should reflect the change.
- Yarn counter. Small device with convex glass for counting the yarn for quality.
Conclusion:
This may be the basic guideline for the piece goods inspection and verification. One may go deeper into the procedure and try to control things in better way.