Now You Know Dyeing Cotton Knit Goods without Bleaching (Part-2)
Monday, 4 February 2019
Edit
Scope of Dyeing Cotton Knit Goods without Bleaching Operation for Energy Saving and Cost Reduction (Part-2)
Md. Palash Hossain
Department of Textile Engineering
Dhaka University of Engineering & Technology (DUET)
Email: palashsakal@yahoo.com
Department of Textile Engineering
Dhaka University of Engineering & Technology (DUET)
Email: palashsakal@yahoo.com
Previous Part
2.2 Methods:
Method followed: Exhaust Method
2.2.1 PROCESSES FOLLOWED IN LABORATORY TRIAL:
A. Pretreatment:
Table 6: Recipe for pretreatment
With Bleaching | Without Bleaching | |||
Name of chemicals | Quantity (g/l) | Name of chemicals | Quantity (g/l) | |
Wetting agent | 1.5 | Wetting agent | 1.5 | |
Sequestering agent | 1.5 | Sequestering agent | 1.5 | |
Caustic soda (NaOH) | 5 | Caustic soda (NaOH) | 5 | |
Hydrogen peroxide(H2O2) | 5 | - | - | |
Stabilizer | 1.5 | - | - | |
Peroxide killer | 0.05 | - | - | |
M:L | 1:10 | M:L | 1:10 | |
Temperature | 100oc | Temperature | 100oc |
Sequence followed in scouring & bleaching:
![]() |
Figure-1: Scouring and bleaching procedure scheme in IR lab dyeing machine |
![]() |
Figure-2: Scouring without bleaching procedure scheme in IR lab dyeing machine |
All the chemicals were taken according to recipe. 10% stock solution of caustic soda was prepared. Then the samples were given in scouring bath. The program was set for 40 min at 1050c. After unloading of the samples normal wash were done for 5 minutes. Then peroxide killer was used in conventional way for removing H2O2 from the fabric at 800c for 15-20 min. After that acid wash was done for the both samples for 10 min. Then hot wash was performed with detergent for 10 min at 800c. Finally cold wash was done.
![]() |
Figure-3: Infra Red lab dyeing machine |
Table 7: Recipe for lab dyeing (0.5% shade)
With peroxide treated fabric | Without peroxide treated fabric | |||
Name of chemicals | Amount(g/l) | Name of chemicals | Amount(g/l) | |
Leveling agent | 1.5 | Leveling agent | 1.5 | |
Wetting agent | 1.5 | Wetting agent | 1.5 | |
G. Salt | 25 | G. Salt | 25 | |
Soda ash | 8 | Soda ash | 8 | |
Detergent | 1 | Detergent | 1 |
Working procedure:
Stock solution preparation: During the lab dip, little amount of dyes and other chemicals were required. 1 gm of dye has been taken in 100 ml of warm water and was made as 1% stock solution of dye. Similarly 20% of Na2CO3 (Sodium carbonate) and 20% of Gluber salt solution have been prepared. The formulae below was exercised to get the accurate amount of dyes and chemicals
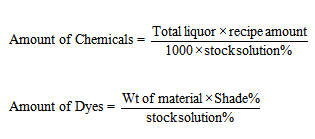
Sample preparation: The pretreated fabric had been cut and made sample of 5 gm by electronic balance. The sample size was required as rectangular to assess rubbing fastness test. Then all the samples ware soaked in distilled water for few minutes and squeezed well which then got ready for dyeing.
Dyeing : All the auxiliaries, salt and dyes were placed in dye bath from stock solution and water was taken to maintain 1:10 liquor ratio. Then fabric was added in dye bath at room temperature and run for 5 minute. Temperature was gradually increased (2o/min) up to 60oC. At this temperature the system was run for 15 min and soda dosing was performed for 45 min. After Completing dyeing the dye liquor was drained out.
After treatment: Normal wash was done. Then hot wash was performed at 80oC with detergent for 10 min. Finally cold wash has been done for 5 min followed by drying at 100oc for 20 min.
Sequence followed in laboratory dyeing:
![]() |
Figure- 4: Dyeing procedure scheme in IR lab dyeing machine |
Specification of used machineries:
- Machine name-MCS
- Origin-Italy
- Machine capacity-1500 kg
- Maximum capacity for single jersey-1000 kg
- Maximum Temperature 13000c
- Maximum water capacity-11200 liter
- No. of nozzle-06
Recipe for 1000 kg knitted (S/J) Fabric:
Table 8: Recipe of pretreatment process for bulk production

Working procedure:
Conventional process | Proposed process | |||||
Steps | Tem | Time | Steps | Tem | Time | |
Fabric loading | 20 min | Fabric loading | 20 min | |||
Addition(detergent + seq. agent + anti creasing + stabilizer) | 500c | 5min | Add (detergent + seq. agent ) | 500c | 3 min | |
Caustic dosing | 500c | 5 min | Caustic dosing | 500c | 5 min | |
Rising temperature and addition H2O2 | 700c | 10 min | Rising temperature | 800c | 15 min | |
Rising temperature | 980c | 15 min | Run time | 30 min | ||
Run time | 60 min | Drain out + fill | 5 min | |||
Cooling | 800c | 10 min | Hot wash | 800c | 10 min | |
Drain out + fill | 5min | Drain out + fill | 5 min | |||
Hot wash | 800c | 10 min | Neutralization | 600c | 15 min | |
Drain out + fill | 5 min | Enzymes wash | 550c | 60 min | ||
Peroxide killer | 900c | 10 min | Drain out + fill | 5 min | ||
Drain out + fill | 5 min | Washing | 10 min | |||
Neutralization | 600c | 15 min | Drain out + fill | 5 min | ||
Enzymes wash | 550c | 60 min | ||||
Drain out + fill | 5 min | |||||
Washing | 10 min | |||||
Drain out + fill | 5 min | |||||
Total time | 255 min | Total time | 188 min |
A.Dyeing:
Recipe:
Table 9: Recipe for dyeing and after treatment
Working procedure:
Sequence followed in dying:
Sequence followed in after treatment:
Recipe:
Table 9: Recipe for dyeing and after treatment
Conventional process | Proposed process | |||||
Name of dyes & chemicals | Brand name | g/l | Name of dyes & chemicals | Brand name | g/l | |
Leveling agent | Dekoven-LVR | 1 | Leveling agent | Dekoven-LVR | 0.5 | |
Anticr . agent | Rucolin-JES | 1 | Anticr . agent | Rucolin-JES | 2 | |
A.acid | Ruco Acid | 1 | A.acid | Ruco Acid | 1 | |
G.salt | 30 | A.acid | Ruco Acid | 0.75 | ||
Yellow | Polafix Yellow 3RS | 1.0% | Yellow | Polafix Yellow 3RS | 1.0% | |
Red | Polafix Red 3BS | 0.3% | Red | Polafix Red 3BS | 0.3% | |
Black | Polafix Black B | 0.7% | Black | Polafix Black B | 0.72% | |
Soda | 12 | Soda | 12 | |||
Soaping agent | Albatex-AD | 0.5 | Soaping agent | Albatex-AD | 0.5 | |
Fixing agent | Neofix-R250 | 0.5 | Fixing agent | Neofix-R250 | 0.5 | |
Softener | Sapamine-CWS | 1 | Softener | Sapamine-CWS | 1 |
Working procedure:
Sequence followed in dying:
Conventional Process | Proposed process | |||||
Steps | Tem | Time (min) | Steps | Tem | Time (min) | |
Add leveling | 500c | Add leveling | 500c | |||
Salt dosing | 500c | 10 | Salt dosing | 500c | 10 | |
Color dosing | 500c | 15 | Color dosing | 500c | 15 | |
Run time | 10 | Run time | 10 | |||
Soda ash dosing | 500c | 20 | Soda ash dosing | 500c | 20 | |
Fixation | 600c | 60 | Fixation | 600c | 60 | |
Drain out + fill | 5 | Drain out + fill | 5 | |||
Total time | 120 min | Total time | 120 min |
Sequence followed in after treatment:
Conventional process | Proposed process | |||||
Steps | Tem | Time | Steps | Tem | Time | |
Normal wash | 10 | Normal wash | 10 | |||
Drain out + fill | 5 | Drain out + fill | 5 | |||
Hot wash(soaping) | 800c | 10 | Hot wash(soaping) | 800c | 10 | |
Drain out + fill | 5 | Drain out + fill | 5 | |||
Normal wash | 10 | Normal wash | 10 | |||
Drain out + fill | 5 | Drain out + fill | 5 | |||
Neutralization | 10 | Neutralization | 10 | |||
Drain out + fill | 5 | Drain out + fill | 5 | |||
Fixing | 10 | Fixing | 10 | |||
Drain out + fill | 5 | Drain out + fill | 5 | |||
Softening | 10 | Softening | 10 | |||
Drain out + fill | 5 | Drain out + fill | 5 | |||
Unload | 20 | Unload | 20 | |||
Total time | 110 | Total time | 110 |
2.2.3 PROCESS FOLLOWED IN TESTING
A. Color fastness to wash
Method followed: ISO 105 C03
B. Color fastness to rubbing /crocking
Method followed: EN ISO 105×12
C. Color fastness to perspiration:
Method followed : ISO105E02